JOTS v34n1 - The Impact of Teaching Oxy-Fuel Welding on Gas Metal Arc Welding Skills
The Impact of Teaching Oxy-Fuel Welding on Gas Metal Arc Welding Skills
Sergio D. Sgro, Dennis W. Field and Steven A. Freeman
Industrial technology programs around the country must be sensitive to the demands of manufacturing and industry as they continue to replace “vocational” curriculum with high-tech alternatives. This article examines whether or not teaching oxyacetylene welding in the industrial technology classroom is required to learn arc welding processes. The results of this study suggests that there appears to be little impact, in terms of gas metal arc welding skills, associated with removing oxyacetylene welding from the curriculum. Because the gas metal arc welding industry is growing globally and industrial technology curricula are under time constraints that often limit the amount of time devoted to welding, faculty should consider suspending oxy-fuel welding to allow more time in gas metal arc welding instruction.
Introduction and Background
Many industrial technology programs struggle to identify and institute curricular activities that adequately serve all of the needs of local and regional industry. In light of “new” technologies, such as CNC, CAD/CAM, and the ever-growing robotics and automation markets, it is no surprise that the perceived importance of vocational skills steadily decreases. But the emphasis during the past decades to pursue less physically demanding careers has resulted in profound labor shortages throughout almost all industries ( Brat, 2006 ), particularly manual welding, as evidenced by a recent Wall Street Journal Online Marketplace article:
The average age of welders, currently 54, keeps climbing. As a wave of retirements loom, welding schools and on-site training programs aren't pumping out replacements fast enough. As a result, many companies are going to great lengths to attract skilled welders, sending recruiters to far-away job fairs and dangling unprecedented perks. ( Brat, 2006, p. 10)
Industrial technology programs around the country must be sensitive to the demand for welders as they continue to replace “vocational” curriculum with high-tech alternatives. Entry-level managers who understand the practical as well as the theoretical nature of technology are still required. “The primary distinguishing characteristic of technological knowledge is that it derives from, and finds meaning, in activity” ( Herschbach, 1995, para. 28). Much of the facility and vocational equipment infrastructures in industrial technology programs remain intact, albeit a bit dusty, and they should be utilized to revitalize or reorganize hot metals curricula to meet the demands of industry.
This article delves into welding education as its authors consider which processes, if any, are helpful for the student to learn first if he or she is to become proficient in arc welding. In particular, the researchers have chosen oxy-fuel welding (OFW), also known as oxyacetylene welding, and gas metal arc welding (GMAW) as the two test vehicles. Oxy-fuel welding is the oldest welding process that burns oxygen and acetylene in a flame to melt metal beyond its solid state. It has been largely superseded by arc welding ( American Welding Society [AWS], 2004 ). Gas metal arc welding continues to grow globally ( Pekkari, 2000 ) and is used extensively in “industrial manufacturing, agriculture, construction, shipbuilding and mining” ( AWS, 2004, p. 148). Gas metal arc welding uses an electric power source, rather than a flame, to produce an arc that melts metal beyond its solid state.
Literature Review State of the Welding Industry
“The highly increased consumption of solid wires in 1999 over 1998 by almost 35 percent (in USA) reflects extremely good business conditions” ( Pekkari, 2000, p. 3). Pekkari ( 2000 ) also explained the immense shift from manual metal arc (MMA) (also known as shielded metal arc welding or “stick”) to gas metal arc welding in the last quarter of the 20th century. In 1975, manual metal arc utilized just over 50 percent of all arc welding; by the turn of the century, the number had fallen to approximately 15 percent of arc welding. Contrary to its counterpart’s demise, gas metal arc welding has ballooned from approximately 20 percent of all arc welding to almost 60 percent ( Pekkari, 2000 ). In fact, Pekkari continues this comparison with the following statement, “The number of arc welding applications has continuously been growing since 1975” ( 2000, p. 5). More important, many more shops and manufacturing facilities look to robotic welding for reduced production time and increased quality ( Harris, 2005 ).
In 2002, the U.S. Department of Commerce ( 2002 ) released a study entitled “Welding- Related Expenditures, Investments, and Productivity in U.S. Manufacturing, Construction, and Mining Industries.” The first two major findings of the report represent credible evidence regarding this study that industrial technology students must be adequately prepared to manage current welding technology as effectively as possible within the limited time allotted in the classroom. Those findings are as follows ( U.S. Department of Commerce, 2002, p. 1):
- Welding expenditures represent a substantial contribution to the U.S. economy.
- By far, labor represents the largest proportion of total welding expenditures.
Recently, The Wall Street Journal Online Edition published an article describing how manufacturers, both large and small, are dealing with a shortage in qualified welders ( Brat, 2006 ).
From an educational standpoint, teachers also should be prepared to purchase or update existing equipment that will aid in the preparation of the managers. The need to consider costs is an important component of curriculum considerations.
Cost Considerations for the Metals Lab
Incurred costs fall under four areas: equipment costs, energy costs, labor costs, and material costs ( AWS, 2004 ). Of particular interest to this research are equipment costs and student contact time (actual time welding) on the equipment. The following is a general introduction to the equipment and its use.
Oxy-fuel Welding Equipment
Oxy-fuel welding equipment, also known as oxygen acetylene welding, is relatively inexpensive, portable, and versatile ( AWS, 2004, ). It is used for welding, cutting, brazing, and soldering.A proportionally equal mixture of oxygen and acetylene is burned at a temperature of 5,589º Fahrenheit ( Althouse, Turnquist, Bowditch, Bowditch, & Bowditch, 2003 ). Equipment costs, excluding rented gas cylinders, can range from several hundred dollars (torch outfit and gas regulators) to approximately $1,000.00.
Students must first learn to light the oxy-fuel flame, adjust the neutral flame, and heat up the base metal before beginning to weld. These steps alone, notwithstanding the dangers and nuances of gas regulators and the addition of filler metal, can absorb a lot of class time. This is especially critical for schools that have limited space and limited time in the curriculum allocated to welding. In this situation, a student could spend most of his or her time adjusting the flame, heating up the base metal, or trying to understand the two-handed coordination of creating a puddle, adding filler material, and moving the puddle.
Gas Metal Arc Welding Equipment
Unlike oxy-fuel welding, gas metal arc welding equipment can range from about $2,500 for a stand-alone welder up to $9,000 for a multi-process welding machine. Most gas metal arc welders now come equipped with recommended weld settings for wire speed and voltage. Students are generally able to quickly set dials or similar apparatuses to the intended material thickness and begin welding. No time is needed to adjust the flame, heat up the base metal, or learn how to add filler material into the weld puddle; this is done automatically.
Travel speed comparison
Given that welding is a physical activity, an important function in student learning is allotting as much practice time as possible. One aspect of this learning time can be a function of the welding travel speed. “Travel speed is defined as the linear rate at which the arc is moved along the weld joint” ( AWS, 2004, p. 183). Table 1 is an approximate travel speed comparison between oxy-fuel and gas metal arc welding of 0.1875 inch mild steel thick plate. Some of the time difference between welding types is attributed to heating up the base metal and changing or replenishing filler material in oxy-fuel welding, but most important is the welding speed.
Welding Type | Approximate travel speed (inches per minute) |
---|---|
Oxy-fuel gas welding | 2.8 ( Althouse, et al, 2003 ) |
Gas metal arc welding | 20 - 22 ( AWS, 2004 ) |
Welding Education
Industrial technology students are generally exposed to oxy-fuel welding, shielded metal arc welding, and gas metal arc welding in materials and processes courses. At some institutions, students are asked to perform a practical test to demonstrate a certain level of competency in one or more of these welding processes. It is useful to examine different approaches to welding as it is viewed by several well-known welding schools.
There are many welding schools around the country, but these schools typically teach according to some standard curriculum, usually benchmarking to the American Welding Society’s conventions. Given that oxy-fuel welding was the first type of welding and that the process has not changed in over a century ( AWS, 2004 ), it is no wonder that the basic method of teaching welding (from oxy-fuel to arc welding) is still practiced today ( Sosnin, 1982 ). This section gives a brief curriculum overview of the larger, well-known national welding schools with special focus on oxy-fuel and gas metal arc welding. For instance, the Hobart Institute for Welding Technology [HIWT] ( 2005 ) has made efforts to upgrade their video/DVD training modules to incorporate current teaching techniques. In particular, the online description of their 24-module GMAW introductory course includes the following overview:
Each skill module includes a demonstration of the weld that students are expected to perform, featuring dramatic, close-up shots of the arc and puddle. Theory modules contain all the essential information associated with the gas metal arc welding process, and feature attractive animated graphics to illustrate key concepts. Male and female narrators alternate throughout, to maintain student interest and highlight key points (¶ 2).
Modern Welding ( Althouse, et al., 2003 ), a complete entry-level textbook, correlates the entire book and its chapters to the American Welding Society’s Guide for Training and Qualification of Welding Personnel – Entry Level Welder learning objectives. These objectives include:
- Occupational Orientation
- Drawing and Weld Symbol Interpretation
- Arc Welding Principles and Practices
- Oxy-fuel Gas Cutting Principles and Practices
- Arc Cutting Principles and Practices
- Welding Inspection and Testing Principles
It should be noted that oxy-fuel welding is not a principle learning objective but rather a subset of the oxy-fuel gas cutting learning objectives.
Lincoln Electric’s Lincoln Welding School ( n.d. ) covers only the fundamentals of oxy-fuel welding in the introduction to their plasma, oxy-fuel, alloy, and hardening course description.
Need for the Study
Sosnin ( 1982 ) summarizes the prevailing anecdotal evidence uncovered by the researchers during conversations and classroom lectures with various vocational instructors regarding welding education: “It has been proven, many times, that when a student learns to weld with an oxyacetylene torch first, he learns to weld quicker and better with the other processes” (p. 48). Unfortunately, no data or research has been uncovered to support that notion. Furthermore, Depue and Pollock (personal communication, October 5, 2005), both American Welding Society (AWS) Educational Division directors, disagreed with the statement unless it was applied exclusively to gas tungsten arc welding, also known as TIG welding. Sosnin ( 1982 ) also indicates that oxyacetylene welding (also known as oxy-fuel gas welding) is a traditional method that should be utilized as much as possible in production for economic and efficiency benefits. However, literature that is more current limits the extent of oxy-fuel welding to maintenance and repair exclusively ( AWS, 2004 )
Today’s manual welding industry depends largely on arc welding technology ( AWS, 2004 ), and despite the technological growth of robotic arc welding equipment, there remains a growing need for skilled welders ( Althouse, et al., 2003 ; Brat, 2006 ). For the industrial technologist, this means, as part of their formal education, more experience is needed for arc welding processes that are currently employed throughout industry in order for them to become better managers of those technologies. As stated previously, many scholars and tradesmen of the vocational era apparently still believe that oxy-fuel welding is the most critical welding process to learn; however, Dolby ( 2003 ) found that arc welding has been the primary welding source for half a century. In particular, he stressed its dominance in the engineering construction sector. This is further warranted by the lack of literature pertaining to the use of oxy-fuel welding. For example:
- Air Products, PLC ( 1999 ) published its Welder’s Handbook without any mention of oxy-fuel welding, only oxy-fuel gas cutting.
- Deposition rates and economic sections of welding books and handbooks compare different arc welding processes, but none reviewed compare arc welding to oxy-fuel welding (Depue & Pollock, personal communication, October 5, 2005).
- Early on, it was recognized that welding repair and maintenance work was inherently not steady ( Plumley, 1949 ); a reality the researcher (Sgro) has experienced firsthand as a metal worker over fifty years later.
- In their Curriculum Guide for the Training of Welding Personnel: Level 1 - Entry Level ( AWS, 2005 ), oxy-fuel welding is not included as a part of the recommended entry-level welder profile.
To that end, there is a disparity between Sosnin’s ( 1982 ) assumption regarding the sequence of the welding curriculum versus the direction, and more important, the perceived needs for technical managers of welding in industry. It is the researchers’ belief that there are a number of schools that continue to stress the importance of oxy-fuel welding, and its direct benefits to arc welding, without the use of empirical data to support the assumption. To that end, the question becomes: Should faculty devote limited time and resources in industrial technology classes to this technology? This research answers this question both empirically and through literature of current trends in the welding industry.
Purpose of the Study
This study aims to identify whether or not teaching oxy-fuel welding prior to gas metal arc welding, also known as metal inert gas “MIG” welding, under classroom conditions significantly improves gas metal arc welding skills for industrial technology students in a National Association of Industrial Technology (NAIT) accredited, four-year institution. Classroom conditions refer to typical teaching conditions encountered by the students in industrial technology.
Given the advances and enormity of the welding industry (especially in automatic, plastics, and specialty alloy welding), the research was focused on oxy-fuel and gas metal arc welding for the following reasons:
- “Oxyacetylene is one of the oldest welding processes” ( AWS, 2004, p. 468).
- It was noted that many vocational scholars asserted and still believe learning oxy-fuel welding before arc welding is imperative ( Sosnin, 1982 ).
- Gas metal arc welding has a higher metal deposition rate than either shielded metal arc welding (SMAW – also known as “stick welding”) and gas tungsten arc welding (GTAW – also known as “TIG welding”) ( Althouse, et al., 2003 ), a fact that directly affects student practice.
- No literature has been uncovered that compares oxy-fuel welding directly to gas metal arc welding (Depue & Pollock, personal communication, October 5, 2005).
Many industrial technology programs inherently stress the importance of oxy-fuel welding, and students continue to spend limited class time trying to adequately master the technique.
Research Question
Is there a statistically significant difference in the ability to gas metal arc weld between students who were first taught to oxy-fuel weld (with or without filler) versus those students who were not taught to oxy-fuel weld?
Statistical Hypothesis 1
Ho: μOFW+filler = μOFW-filler = μGMAW
Ha: μOFW+filler ≠ μOFW-filler ≠ μGMAW
Statistical Hypothesis 2
Ho: μOFW(with and without Filler) = μGMAW
Ha: μOFW(with and without filler) ≠ μGMAW
Methodology
Population and Sample
The research was conducted in three sections of an introductory materials processing course (ITEC 130: Production Materials and Processes) in the Department of Industry and Technology at Millersville University in the Spring 2006 semester. The population for this study is industrial technology students with a focus on four-year technical management programs. Each section of the course meets for a total of four hours and 10 minutes of contact time per week. The experiment was conducted during two class periods. During this time, each class was given lecture, manipulative/practice time, and a final gas metal arc welding test. Given that this is all the time that is allotted to welding during other semesters at Millersville University (and sometimes less), it provides an opportunity to perform the experiment under the time constraints of a normal semester. Furthermore, students are given lab time each week, outside the normal course schedule, to practice their skills (not just welding skills) and to complete projects, if they choose to do so.
Prior to the experiment, a survey was administered to each student to collect information pertaining to any prior welding experience. The survey gathered information about which welding process, if any, the student had previously learned. When a student indicated prior welding experience, he or she was asked to specify between (a) oxyacetylene welding (not oxyacetylene cutting), (b) shielded metal arc welding, (c) gas metal arc welding, (d) gas tungsten arc welding, or (e) some other type not identified above. In addition, those students who indicated prior welding experience were asked to complete how much welding time was spent on the specified welding experience. Three choices were available for each welding process selection, they were: (a) greater than zero but less then two hours of experience, (b) two to twenty hours of welding experience, or (c) greater than 20 hours of experience.
Statistical Design
The study is a one-factor experiment with three treatment groups with two stages of analysis. Stage one is a one-way analysis of variance (ANOVA) with three treatment groups and one factor of interest. The treatment groups and sample sizes can be found in Table 2.
Group/Class | Treatment Groups | Total |
---|---|---|
1 | OFW w/ Filler + GMAW | 24 Students |
2 | OFW w/out Filler + GMAW | 20 Student |
3 | GMAW + GMAW | 24 Students |
On day one of the study, each group was taught and practiced only one type of welding [oxy-fuel with filler (OFW+F), oxy-fuel without filler (OFW-F), or gas metal arc welding (GMAW)]. On day two, each class practiced and was immediately tested on gas metal arc welding. Each weld was independently evaluated by two welding instructors for seven pre-defined characteristics on a 1 to 10 scale. The two evaluators’ scores were averaged for each of the seven scores, and those seven averaged scores were used to compute an overall mean score per student. In order to evaluate the effect of oxy-fuel welding (with and without filler, collectively) on gas metal arc welding skills, the effects of oxy-fuel welding were pooled together and compared to the gas metal arc welding group.
Stage two of the experiment is an evaluation of how students performed on specific parts of the weld. More specifically, it evaluated whether teaching oxy-fuel welding prior to gas metal arc welding significantly improved any gas metal arc welding test characteristics. An analysis of variance with a narrow alpha level (0.01) was used for each individual test. A narrower alpha level for each of the seven tests, called a Bonferroni correction, was used to ensure a higher confidence level overall ( Agresti & Finlay, 1997 ).
The researcher (Sgro) utilized lectures previously given to ITEC 130 students in the Spring 2004 semester when he was an instructor at Millersville University. The lecture material follows the curriculum guide of the American Welding Society (for GMAW only).
Practice
The experiment spanned two class periods. Day one was largely devoted to introduction of welding and practicing the weld process assigned to that particular class. Day two included instruction with a shorter practice time and the actual welding experiment on the gas metal arc welding process. The following procedures describe what was taught and demonstrated in each class, respectively. Given that there were only two oxygen acetylene torch outfits and one gas metal arc welder, practice time was limited to two minutes per student. During the oxy-fuel practice times, lighting and flame adjustment was demonstrated and then the torch was handed to the student. Each student practiced for a total of two minutes. For the class that was taught how to add filler material into the weld puddle, practice time was divided into two parts. One minute was allowed for puddle creation and moving, and one minute was allowed for practicing puddle creation, adding filler material, and then moving the puddle. Those students who did not have any oxy-fuel training practiced for two minutes on gas metal arc welding.
Testing
On the second day of the experiment, each group was given the same practice/testing sequence on gas metal arc welding. Every student practiced for one minute on an unmarked lap joint. Immediately following the one minute of practice, the students welded the test specimen lap joint to the best of their ability. There was no guidance during the final welding test. An example of the lap joint test specimen is shown in Figure 1. Each student was randomly called to perform the test.
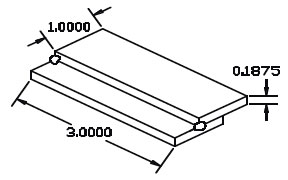
An Airco Dip-Pak 250 welder was used for practice and testing of all participants. The welder was set to the manufacturer’s recommended short-circuiting arc voltage and wire feed for 0.1875 inch thick mild steel with 0.035 inch diameter wire using 75% Argon – 25% Carbon Dioxide shielding gas. The welder was set to “1” on the medium voltage range and “4” for the wire feed speed. Although the Dip-Pak 250 is no longer manufactured and no manuals for the welder could be found, the actual voltage (20 Volts) and wire feed speed (265 inches per minute) can be estimated using the Typical Conditions for the Gas Metal Arc Welding of Carbon and Low-Alloy Steels in the Flat Position (Short-Circuiting Transfer) of the American Welding Society Welding Handbook ( AWS, 2004, p. 186).
Inspection
Two welding instructors from the Lancaster County Career and Technology Center, Lancaster, Pennsylvania, inspected each test specimen on each of the following seven quality characteristics: (1) Test 1-- weld height, (2) Test 2 - weld width, (3) Test 3 - undercut, (4) Test 4 - uniformity of weld, (5) Test 5 - proper contour, (6) Test 6 - surface contaminants/porosity, and (7) Test 7 - penetration at top. This rubric was developed jointly by the researchers and the welding instructors to identify areas the instructors consider for their beginning students. At this level of competency and practice time, that is, with only a few minutes of practice time, it was not deemed appropriate to perform mechanical testing. Visual inspections determine whether or not the students understand the basic concept of creating and moving a molten weld puddle.
Results
The data table for all seven tests are presented next.
Group | n | Test 1 | Test 2 | Test 3 | Test 4 | Test 5 | Test 6 | Test 7 | Overall Mean | SD |
---|---|---|---|---|---|---|---|---|---|---|
OFW+F | 24 | 3.52 | 2.53 | 7.40 | 3.42 | 2.85 | 7.19 | 5.23 | 4.59 | 1.95 |
OFW-F | 20 | 2.83 | 2.90 | 7.18 | 3.23 | 1.63 | 6.50 | 6.25 | 4.36 | 1.54 |
GMAW | 24 | 4.92 | 3.73 | 6.54 | 4.46 | 3.25 | 7.90 | 6.56 | 5.33 | 1.83 |
Overall | 68 | 3.81 | 3.06 | 7.03 | 3.73 | 2.63 | 7.24 | 6.00 | 4.79 |
The one-way analysis of variance of the overall mean scores between oxy-fuel welding with filler, oxy-fuel welding without filler, and gas metal arc welding indicated no significant differences at the 0.05 alpha level (p = 0.168).
Source | df | F |
---|---|---|
Note. *p < .05. | ||
Instructional Method | 2 | 1.835 |
Error | 65 |
A subsequent analysis comparing oxy-fuel welding, with and without filler, versus gas metal arc welding was performed using the least squares contrast function of JMP 6.0 ( SAS Institute, 2005 ) with coefficients of -0.5, -0.5, and 1 for oxy-fuel welding with filler, oxy-fuel welding without filler, and gas metal arc welding, respectively. The contrast compares the averages of the oxy-fuel welding groups, collectively, to the third group, gas metal arc welding, utilizing the pooled estimate of variance for all three groups. Based on the contrast test, there is no significant difference in overall welding scores between those students who first learned to oxy-fuel weld versus those students who did not learn to oxy-fuel weld.
Source | df | F |
---|---|---|
Note. *p < .05. | ||
Instructional Method | 1 | 3.562 |
Error | 65 |
Given that the overall mean scores are made up of the seven individual test scores, a one-way analysis of variance was performed to assess whether any of the seven welding characteristics tested were significantly different between the oxy-fuel and gas metal arc welding groups. In this analysis, oxy-fuel welding with filler and oxy-fuel welding without filler were once again contrast (n = 44) and compared to the gas metal arc welding group (n = 24). Each of the seven tests was performed on the weld specimens thereby making each test dependant on the other six tests. An adjustment was made for simultaneous confidence intervals with alpha = 0.01 for each individual test (this is an approximation for the Bonferroni correction: 0.05/7 = 0.00714) for an approximate total margin of error equal to 0.05. The analysis of variance results for each weld test are presented below.
Source | df | F |
---|---|---|
Note. **p < .01. | ||
Test 1 | 1 | 7.734** |
Test 2 | 1 | 2.621 |
Test 3 | 1 | 2.960 |
Test 4 | 1 | 4.490 |
Test 5 | 1 | 4.635 |
Test 6 | 1 | 2.917 |
Test 7 | 1 | 1.470 |
Error | 65 error term applies to each test |
Of the seven weld characteristics evaluated, Test 1 (weld height) was the only characteristic statistically significant at the 0.01 alpha level (p = 0.007). For Test 1, those students who were taught gas metal arc welding scored higher than those students who were taught how to oxy-fuel weld first. Test 2 through Test 7 were all found to be not significant at the 0.01 level: there was no significant difference between those students who were taught oxy-fuel welding versus those who were not taught oxy-fuel welding. The error term in the analysis of variance table above is 65 degrees of freedom per test. A graph of the mean scores for each of the seven tests is shown in Figure 2.
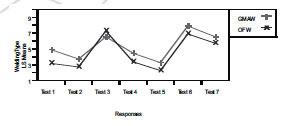
The graph illustrates that on average, students tend to weld better in certain areas than they do in others, regardless of their initial welding instruction.
Discussion
The results of this research revealed that there is no statistically significant overall difference in arc welding skills between those students who were first taught to oxy-fuel weld versus those who were not taught to oxy-fuel weld. In fact, of the seven individual characteristic tests on each weld specimen, one individual weld test suggested that students who did not oxy-fuel weld performed better than those who were taught to oxy-fuel weld (p = 0.007). Under the conditions of this research, the outcomes did not support Sosnin’s ( 1982 ) assertion that students learned to weld other processes better and faster if they were first taught to oxy-fuel weld. To that end, recommendations are presented in support of an industrial technology welding curriculum without the use of oxy-fuel welding. It should be noted that these recommendations are for industrial technology programs whose main focus is technology management, when time constraints must be considered, not welding. The outcome of the research does not affect or impede the importance of learning oxy-fuel welding when gas tungsten arc welding or oxy-fuel welding and cutting will be a significant skill set the student will learn for his or her profession.
From the surveys given before the experiment, over half of the students had no previous welding experience. Some students indicated some experience in either oxy-fuel welding, shielded metal arc welding, gas metal arc welding, and/or gas tungsten arc welding. Although it makes sense to account for experience statistically (those with more experience scored significantly higher), it is typically not practical to separate those in an industrial technology class into those with and without experience. Additionally, sample sizes for the experience covariate, especially specific experience in any of the aforementioned categories, were reason for concern and were therefore not included in this analysis.
The literature pointed to a global increase in gas metal arc welding solid wire consumption ( Pekkari, 2000 ). This is further supported by the U.S. Department of Commerce’s ( 2002 ) findings that welding expenditures make up a substantial contribution to our economy, especially the labor portion, as well as a recent Wall Street Journal Online Edition ( Brat, 2006 ) citing the present welding labor shortages. These economic indicators, coupled with the time a student can spend learning arc welding skills, call for efficient and effective instructional methodologies when time is limited.
One can argue that oxy-fuel welding equipment is significantly less expensive, but the cost of the equipment versus the time students spend creating and moving puddles is generally ignored. Based on the material thickness and travel speed time figures presented in the literature review, a student using gas metal arc welding can weld over seven times the amount of linear distance than a student using oxy-fuel welding. These numbers are conservative given that they do not include learning curves for understanding how to properly light and adjust a torch, as well as the coordination required to add filler material with a second hand. Generally speaking, welding schools no longer teach oxy-fuel welding as a major welding component, but rather they incorporate it into a cutting and brazing program.
Future research in welding education is recommended to better understand where the true differences in learning each type of welding exist. This study indicated that those who were taught only gas metal arc welding performed better on welding height, but why? Subsequent studies should focus on longer practice time for both types of welding, whereby true welding skills are developed and then tested using both destructive test methods, such as tensile tests or bend tests, as well as nondestructive and visual tests. Experiments should be set up to effectively evaluate different aspects of the weld (height, undercut, porosity, etc.) as well as strength and penetration. One suggestion to validate the findings of this research would be to increase the sample size of the groups and perform multiple tests on students as more practice is given to improve their skills. In doing so, researchers can better understand where beginning welders are typically stronger or where better teaching methods are required. Understanding where students struggle can be a powerful mechanism for streamlining the initial learning of welding. The field of Industrial technology could benefit immensely in terms of time and program effectiveness by teaching welding more efficiently.
Technology programs, in particular those with welding, must keep students and industry in mind – this means that gas metal arc welding is a critical component of the industrial technology curriculum.
Dr. Sergio Sgro is an Assistant Professor in the Department of Technology at Eastern Kentucky University, Richmond, and is a member of the Alpha Xi Chapter of Epsilon Pi Tau.
Dr. Dennis Field is a Professor and Coordinator of the Industrial Technology program in the Department of Technology at Eastern Kentucky University, Richmond, and is a member of the Alpha Xi Chapter of Epsilon Pi Tau.
Dr. Steven A. Freeman is a Professor in the Department of Agricultural and Biosystems Engineering and Assistant Director of the Center for Excellence in Learning and Teaching at Iowa State University, Ames. He is a member of the Alpha Xi Chapter of Epsilon Pi Tau.
References
Agresti, A & Finlay B (1997). Statistical methods for the social sciences (3rd ed.). Upper Saddle River, NJ: Prentice-Hall.
Air Products PLC (1999). Welder's handbook for gas shielding arc welding, oxy fuel cutting & plasma cutting (3rd ed.). Air Products PLC.
Althouse, A. D., Turnquist, C. H., Bowditch, W. A., Bowditch, K. E., & Bowditch, M. A. (2003). Modern welding. Tinley Park, IL: Goodheart-Wilcox.
American Welding Society [AWS]. (2004). In A. O’Brien (Ed.). Welding handbook (9th ed.): Vol. 2, Welding Processes, Part 1. Miami, FL: American Welding Society.
American Welding Society (2005). Curriculum guide for the training of welding personnel: Level I - entry level (Draft). Unpublished manuscript.
Brat, I. (2006). Where have all the welders gone, As manufacturing and repair boom? Wall Street Journal Online. Retrieved August 18, 2006, from http://webreprints.djreprints.com/1531490511822.html.
Dolby, R. E. (2003). Trends in welding processes in engineering construction for infrastructure projects. Paper presented at the 56th IIW Annual Assembly, 6 - 11 July 2003, Bucharest, Romania.
Harris, R. (2005). Creating competitive businesses. [Electronic version] Welding Design and Fabrication, 78, 4.
Herschbach, D. R. (1995) Technology as knowledge: Implications for instruction [Electronic version from digital libraries and archives]. Journal of Technology Education, 5, Retrieved August 20, 2006, from http://scholar.lib.vt.edu/ejournals/JTE/v7n1/herschbach.jte-v7n1.html.
Hobart Institute of Welding Technology [HIWT]. (2005). HIWT Gas metal arc welding basic (GMAWB). Retrieved November 8, 2005, from http://www.welding.org/cart/training/gmawb.htm
Lincoln Electric (n.d.) The Lincoln Welding School. Plasma Oxy-Fuel, Alloy, & Hardfacing. Retrieved September 4, 2006, from http://content.lincolnelectric.com//pdfs/knowledge/training/weldschool/LWSAlloy.pdf.
Pekkari, B. (2000, November). Trends in joining, cutting, and a sustainable world. Paper presented at The Richard Weck Lecture at the Institute of Materials, London, UK.
Plumley, S. (1949). Oxyacetylene welding and cutting (4th ed.). New York: McGraw-Hill.
SAS Institute Inc. (2005). JMP (Version 6.0.0) [Computer software]. Cary, NC: SAS Institute.
Snedecor, G. W. & Cochran, W. G. (1989). Statistical methods (8th ed.). Ames, IA: Iowa State University Press.
Sosnin, H. A. (1982). Efficiency and economy of the oxyacetylene process. The Welding Journal, 61, 46-48.
U.S. Department of Commerce, Bureau of Export Administration, Office of Strategic Industries & Economic Security (2002). Welding-related expenditures, investments, and productivity in U.S. manufacturing, construction, and mining industries. (OMB Control No. 0694-0019, Ref. No. 1WAAELIM). Washington, DC: U.S. Department of Commerce. (Available Online at http://www.aws.org/research/HIM.pdf).
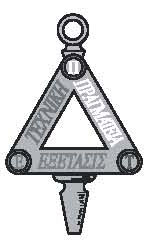
TS