JOTS v35n1 - Potential Ambient Energy-Harvesting Sources and Techniques
Potential Ambient Energy-Harvesting Sources and Techniques
Faruk Yildiz
Abstract
Ambient energy harvesting is also known as energy scavenging or power harvesting, and it is the process where energy is obtained from the environment. A variety of techniques are available for energy scavenging, including solar and wind powers, ocean waves, piezoelectricity, thermoelectricity, and physical motions. For example, some systems convert random motions, including ocean waves, into useful electrical energy that can be used by oceanographic monitoring wireless sensor nodes for autonomous surveillance. Ambient energy sources are classified as energy reservoirs, power distribution methods, or power-scavenging methods, which may enable portable or wireless systems to be completely battery independent and self sustaining. The students from different disciplines, such as industrial technology, construction, design and development and electronics, investigated the effectiveness of ambient energy as a source of power. After an extensive literature review, students summarized each potential ambient energy source and explained future energy-harvesting systems to generate or produce electrical energy as a support to conventional energy storage devices. This article investigates recent studies about potential ambient energy-harvesting sources and systems.
Introduction
Today, sustaining the power requirement for autonomous wireless and portable devices is an important issue. In the recent past, energy storage has improved significantly. However, this progress has not been able to keep up with the development of microprocessors, memory storage, and wireless technology applications. For example, in wireless sensor networks, battery-powered sensors and modules are expected to last for a long period of time. However, conducting battery maintenance for a large-scale network consisting of hundreds or even thousands of sensor nodes may be difficult, if not impossible. Ambient power sources, as a replacement for batteries, come into consideration to minimize the maintenance and the cost of operation. Power scavenging may enable wireless and portable electronic devices to be completely self-sustaining, so that battery maintenance can be eventually removed. Researchers have performed many studies in alternative energy sources that could provide small amounts of electricity to electronic devices, and this will be explained in another section of this article.
Energy harvesting can be obtained from different energy sources, such as mechanical vibrations, electromagnetic sources, light, acoustic, airflow, heat, and temperature variations. Energy harvesting, in general, is the conversion of ambient energy into usable electrical energy. When compared with energy stored in common storage elements, such as batteries, capacitors, and the like, the environment represents a relatively infinite source of available energy.
Systems continue to become smaller, yet less energy is available on board, leading to a short run-time for a device or battery life. Researchers continue to build high-energy density batteries, but the amount of energy available in the batteries is not only finite but also low, which limits the life time of the systems. Extended life of the electronic devices is very important; it also has more advantages in systems with limited accessibility, such as those used in monitoring a machine or an instrument in a manufacturing plant used to organize a chemical process in a hazardous environment. The critical long-term solution should therefore be independent of the limited energy available during the functioning or operating of such devices. Table 1 compares the estimated power and challenges of various ambient energy sources in a recent study by Yildiz, Zhu, Pecen, and Guo (2007) . Values in the table were derived from a combination of published studies, experiments performed by the authors, theory, and information that is commonly available in textbooks. The source of information for each technique is given in the third column of the table. Though this comparison is not comprehensive, it does provide a broad range of potential methods to scavenge and store energy from a variety of ambient energy sources. Light, for instance, can be a significant source of energy, but it is highly dependent on the application and the experience to which the device is subjected. Thermal energy, in contrast, is limited because temperature differences across a chip are typically low. Vibration energy is a moderate source, but again, it is dependent on the particular application, as cited by Torres and Rincon-Mora (2005) .
Energy Source | Power Density & Performance | Source of Information |
---|---|---|
Acoustic Noise |
0.003 μW/cm3 @ 75Db
0.96 μW/cm3 @ 100Db |
(
Rabaey, Ammer, Da Silva Jr,
Patel, & Roundy, 2000 ) |
Temperature Variation | 10 μW/cm3 |
(
Roundy, Steingart, Fréchette,
Wright, Rabaey, 2004 ) |
Ambient Radio Frequency | 1 μW/cm2 | ( Yeatman, 2004 ) |
Ambient Light |
100 mW/cm2 (direct sun)
100 _W/cm2 (illuminated office) |
Available |
Thermoelectric | 60 _W/cm2 | ( Stevens, 1999 ) |
Vibration
(micro generator) |
4 _W/cm3 (human motion—Hz)
800 _W/cm3 (machines—kHz) |
(
Mitcheson, Green, Yeatman,
& Holmes, 2004 ) |
Vibrations (Piezoelectric) | 200 μW/cm3 | ( Roundy, Wright, & Pister, 2002 ) |
Airflow | 1 μW/cm2 | ( Holmes, 2004 ) |
Push buttons | 50 _J/N | ( Paradiso & Feldmeier, 2001 ) |
Shoe Inserts | 330 μW/cm2 | ( Shenck & Paradiso, 2001 ) |
Hand generators | 30 W/kg | ( Starner & Paradiso, 2004 ) |
Heel strike | 7 W/cm2 |
(
Yaglioglu, 2002
)
( Shenck & Paradiso, 2001 ) |
Ambient Energy Sources
Ambient energy harvesting, also known as energy scavenging or power harvesting, is the process where energy is obtained and converted from the environment and stored for use in electronics applications. Usually this term is applied to energy harvesting for low power and small autonomous devices, such as wireless sensor networks, and portable electronic equipments. A variety of sources are available for energy scavenging, including solar power, ocean waves, piezoelectricity, thermoelectricity, and physical motions (active/passive human power). For example, some systems convert random motions, including ocean waves, into useful electrical energy that can be used by oceanographic monitoring wireless sensor nodes for autonomous surveillance.
The literature review shows that no single power source is sufficient for all applications, and that the selection of energy sources must be considered according to the application characteristics. Before going into details, a general overview of ambient energy sources are presented, and summarized the resources according to their characteristics:
- Human Body: Mechanical and thermal (heat variations) energy can be generated from a human or animal body by actions such as walking and running;
- Natural Energy: Wind, water flow, ocean waves, and solar energy can provide limitless energy availability from the environment;
- Mechanical Energy: Vibrations from machines, mechanical stress, strain from high-pressure motors, manufacturing machines, and waste rotations can be captured and used as ambient mechanical energy sources;
- Thermal Energy: Waste heat energy variations from furnaces, heaters, and friction sources;
- Light Energy: This source can be divided into two categories of energy: indoor room light and outdoor sunlight energy. Light energy can be captured via photo sensors, photo diodes, and solar photovoltaic (PV) panels; and
- Electromagnetic Energy: Inductors, coils, and transformers can be considered as ambient energy sources, depending on how much energy is needed for the application.
Additionally, chemical and biological sources and radiation can be considered ambient energy sources. Figure 1 shows a block diagram of general ambient energy-harvesting systems. The first row shows the energy-harvesting sources. Actual implementation and tools are employed to harvest the energy from the source are illustrated in the second row. The third row shows the energy-harvesting techniques from each source. The research efforts are employed by the above listed sources to explore in general how practical devices that extract power from ambient energy sources are. A broad review of the literature of potential energy-scavenging methods has been carried out by the authors. The result of this literature review is categorized for each source, and follows in the next few sections of this paper.
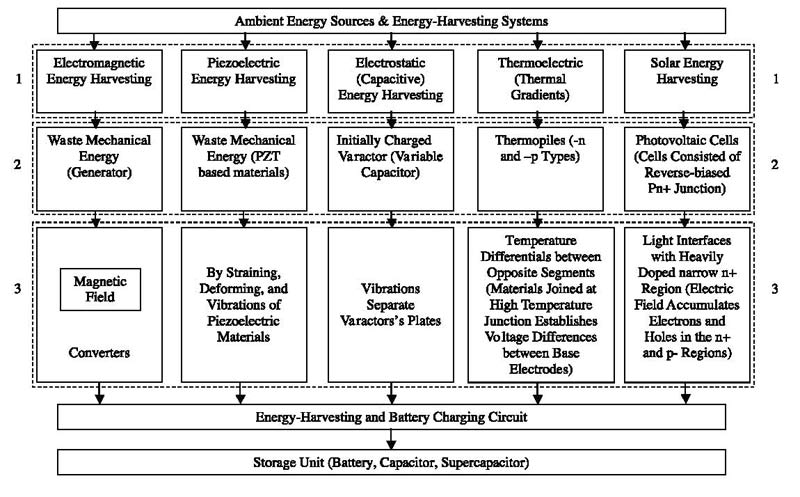
Mechanical Energy Harvesting
An example of electric power generation using rotational movement is the self-powered, battery-less, cordless wheel computer mouse cited by Mikami, Tetsuro, Masahiko, Hiroko (2005) . The system is called Soc and is designed as an ultra low power wireless interface for short-range data communication as a wireless battery-less mouse. The system was designed uniquely to capture rotational movements by the help of the mouse ball to generate and harvest electric power. The electric generator is powered through exploiting rolling energy by dragging the mouse. The energy-harvesting system was intended to power the electronic system of a mouse device, such as the ultra low power RF transmitter and microcontroller. The experimental results of the study showed that the mouse only needed 2.2mW energy to operate. The total energy captured using an energy-harvesting system was bigger than 3mW, which was enough for the wireless mouse operations in a transmit range of one meter.
Another example of mechanical energy harvesting is an electrets-based electrostatic micro generator, which was proposed by Sterken, Fiorini, Baert, Puers, and Borghs (2003) . In this system, a micro machined electrostatic converter consisted of a vibration sensitive variable capacitor polarized by an electret. A general multi domain model was built and analyzed in the same study, and it showed that power generation capabilities up to 50μw for a 0.1cm2 surface area were attainable.
Mechanical Vibrations
Indoor operating environments may have reliable and constant mechanical vibration sources for ambient energy scavenging. For example, indoor machinery sensors may have plentiful mechanical vibration energy that can be monitored and used reliably. Vibration energyharvesting devices can be either electromechanical or piezoelectric. Electromechanical harvesting devices, however, are more commonly researched and used. Roundy, Wright, and Rabaey (2004) reported that energy withdrawal from vibrations could be based on the movement of a spring-mounted mass relative to its support frame. Mechanical acceleration is produced by vibrations that, in turn, cause the mass component to move and oscillate. This relative dislocation causes opposing frictional and damping forces to be applied against the mass, thereby reducing and eventually extinguishing the oscillations. The damping force energy can be converted into electrical energy via an electric field (electrostatic), magnetic field (electromagnetic), or strain on a piezoelectric material. These energy conversion schemes can be extended and explained under the three listed subjects because the nature of the conversion types differs even if the energy source is vibration. In the section below, the main differences of the three sources are discussed.
Electromagnetic
This technique uses a magnetic field to convert mechanical energy to electrical energy ( Amirtharajah & Chandrakasan, 1998 ). A coil attached to the oscillating mass is made to pass through a magnetic field, which is established by a stationary magnet, to produce electric energy. The coil travels through a varying amount of magnetic flux, inducing a voltage according to Faraday's law. The induced voltage is inherently small and therefore must be increased to become a viable source of energy. ( Kulah & Najafi, 2004 ). Techniques to increase the induced voltage include using a transformer, increasing the number of turns of the coil, or increasing the permanent magnetic field ( Torres & Rincón-Mora, 2005 ). However, each of these parameters is limited by the size constraints of the microchip as well as its material properties.
Piezoelectric
This method alters mechanical energy into electrical energy by straining a piezoelectric material ( Sodano, Inman, & Park, 2004 ). Strain or deformation of a piezoelectric material causes charge separation across the device, producing an electric field and consequently a voltage drop proportional to the stress applied. The oscillating system is typically a cantilever beam structure with a mass at the unattached end of the lever, which provides higher strain for a given input force ( Roundy & Wright, 2004 ). The voltage produced varies with time and strain, effectively producing an irregular AC signal on the average. Piezoelectric energy conversion produces relatively higher voltage and power density levels than the electromagnetic system. Moreover, piezoelectricity has the ability of some elements, such as crystals and some types of ceramics, to generate an electric potential from a mechanical stress ( Skoog, Holler, & Crouch, 2006 ). This process takes the form of separation of electric charge within a crystal lattice. If the piezoelectric material is not short circuited, the applied mechanical stress induces a voltage across the material. There are many applications based on piezoelectric materials, one of which is the electric cigarette lighter. In this system, pushing the button causes a spring-loaded hammer to hit a piezoelectric crystal, and the voltage that is produced injects the gas slowly as the current jumps across a small spark gap. Following the same idea, portable sparkers used to light gas grills, gas stoves, and a variety of gas burners have built-in piezoelectric based ignition systems.
Electrostatic (Capacitive)
This method depends on the variable capacitance of vibration-dependent varactors. ( Meninger, Mur-Miranda, Amirtharajah, Chandrakasan, & Lang, 2001 ). A varactor, or variable capacitor, which is initially charged, will separate its plates by vibrations; in this way, mechanical energy is transformed into electrical energy. Constant voltage or constant current achieves the conversion through two different mechanisms. For example, the voltage across a variable capacitor is kept steady as its capacitance alters after a primary charge. As a result, the plates split and the capacitance is reduced, until the charge is driven out of the device. The driven energy then can be stored in an energy pool or used to charge a battery, generating the needed voltage source. The most striking feature of this method is its IC-compatible nature, given that MEMS (Micro-electromechanical system) variable capacitors are fabricated through relatively well-known silicon micro-machining techniques. This scheme produces higher and more practical output voltage levels than the electromagnetic method, with moderate power density.
In a study conducted to test the feasibility and reliability of the different ambient vibration energy sources by Marzencki (2005) , three different vibration energy sources (electrostatic, electromagnetic, and piezoelectric) were investigated and compared according to their complexity, energy density, size, and encountered problems. The study is summarized in Table 2.
Electrostatic | Electromagnetic | Piezoelectric | |
---|---|---|---|
Complexity of process flow | Low | Very High | High |
Energy density | 4 mJ cm-3 | 24.8 mJ cm-3 | 35.4 mJ cm-3 |
Current size | Integrated | Macro | Macro |
Problems |
Very high voltage and need
of adding charge source |
Very low output
voltages |
Low output
voltages |
Thermal (Thermoelectric) Energy Harvesting
Thermal gradients in the environment are directly converted to electrical energy through the Seebeck (thermoelectric) effect, as reported by Disalvo (1999) and Rowe (1999) . Temperature changes between opposite segments of a conducting material result in heat flow and consequently charge flow since mobile, high-energy carriers diffuse from high to low concentration regions. Thermopiles consisting of n- and p-type materials electrically joined at the high-temperature junction are therefore constructed, allowing heat flow to carry the dominant charge carriers of each material to the low temperature end, establishing in the process a voltage difference across the base electrodes. The generated voltage and power is relative to the temperature differential and the Seebeck coefficient of the thermoelectric materials. Large thermal gradients are essential to produce practical voltage and power levels ( Roundy, Wright, & Rabaey, 2004 ). However, temperature differences greater than 10°C are rare in a micro system, so consequently such systems generate low voltage and power levels. Moreover, naturally occurring temperature variations also can provide a means by which energy can be scavenged from the environment with high temperature. Stordeur and Stark (1997) have demonstrated a thermoelectric micro device, which is capable of converting 15 _W/cm3 from 10 °C temperature gradients. Although this is promising and, with the improvement of thermoelectric research, could eventually result in more than 15 _W/cm3, situations in which there is a static 10 °C temperature difference within 1 cm3 are, however, very rare, and assume no losses in the conversion of power to electricity.
One of the latest designs of thermoelectric energy harvester is the thermoelectric generator (TEG) designed and introduced by Pacific Northwest National Laboratory (2007) . This new thermoelectric generator is used to convert environmental (ambient) thermal energy into electric power for a variety of applications that necessitates low power use. This thermoelectric energy harvester includes an assembly of very small and thin thermocouples in a unique configuration that can exploit very small (>2°C) temperature variations that are occurring naturally in the environment of the application such as ground to air, water to air, or skin to air interfaces. The body of the TEG consisted of reliable and stable components that provided maintenance free, continuous power for the lifetime of the application claimed by the manufacturer. Depending on the temperature range, the TEG’s electrical output can be changed from a few microwatts to hundreds of milliwatts and more by modifying the design. Applications of this energy-harvesting design are diverse, including automotive performance monitoring, homeland and military security surveillance, biomedicine, and wilderness and agricultural management. It is also documented that the thermoelectric energy harvester may be appropriate for many other stand-alone, low-power applications, depending on the nature of the application.
In addition to PNNL’s patent-pending thermoelectric generator, Applied Digital Solutions Corporation has developed and presented a thermoelectric generator as a commercial product ( PNNL, 2007 ). This thermoelectric generator is capable of producing 40mw of power from 5 °C temperature variations using a device that is 0.5 cm 2 in area and a few millimeters thick ( Pescovitz, 2002 ). This device generates about 1V output voltage, which can be enough for low- power electronic applications. Moreover, the thermal-expansion-actuated piezoelectric generator has also been proposed as a method to convert power from ambient temperature gradients to electricity by Thomas, Clark and Clark (2005) .
Pyroelectricity Energy Harvesting
The “pyroelectric effect” converts temperature changes into electrical voltage or current ( Lang, 2005 ). Pyroelectricity is the capability of certain materials to generate an electrical potential when they are either heated or cooled. As a result of the temperature change, positive and negative charges move to opposite ends through migration (polarized) and thus, an electrical potential is established. Pryroelectric energy-harvesting applications require inputs with time variances which results in small power outputs in energy-scavenging applications. One of the main advantages that pyroelectric energy harvesting has over thermoelectric energy harvesting is that most of the pyroelectric materials or elements are stable up to 1200 °C or more. Stability allows energy harvesting even from high temperature sources with increasing thermodynamic efficiency.
Light Energy (Solar Energy) Harvesting
A photovoltaic cell has the capability of converting light energy into electrical energy ( Kasap, 2001 ; Raffaelle, Underwood, Scheiman, Cowen, Jenkins, Hepp, Harris, & Wilt, 2000 ). Each cell consists of a reverse biased pn+ junction, in which the light crosses with the heavily conservative and narrow n+ region. Photons where the light energy exists are absorbed within the depletion region, generating electron-hole pairs. The built-in electric field of the junction immediately separates each pair, accumulating electrons and holes in the n+ and p regions, respectively, establishing an open circuit voltage. With a load connected, accumulated electrons travel through the load and recombine with holes at the p-side, generating a photocurrent that is directly proportional to the light intensity and independent of the cell voltage. Several research efforts, have been conducted so far have demonstrated that photovoltaic cells can produce sufficient power to maintain a micro system. Moreover, a three-dimensional diode structure constructed on absorbent silicon substrate helps increase efficiency by significantly increasing the exposed internal surface area of the device ( Sun, Kherani, Hirschman, Gadeken, & Fauchet, 2005 ). Overall, photovoltaic energy conversion is a well-known integrated circuit compatible technology that offers higher power output levels, when compared with the other energy-harvesting mechanisms. Nevertheless, its power output is strongly dependent on environmental conditions; in other words, varying light intensity.
Acoustic Noise
Acoustic noise is the result of the pressure waves produced by a vibration source. A human ear detects and translates pressure waves into electrical signals. Generally a sinusoidal wave is referred to as a tone, a combination of several tones is called a sound, and an irregular vibration is referred to as noise. Hertz (Hz) is the unit of sound frequency; 1 Hz equals 1 cycle, or one vibration, per second. The human ear can perceive frequencies between 20 Hz and 20 000 Hz. Acoustic power and acoustic pressure are types of acoustic noise. Acoustic power is the total amount of sound energy radiated by a sound source over a given period of time, and it is usually expressed in Watts. For acoustic pressure, the reference is the hearing threshold of the human ear, which is taken as 20 microPa. The unit of measure used to express these relative sound levels is the Bel or decibel (1 Bel equals 10 decibels). The Bel and decibel are logarithmic values that are better suited to represent a wide range of measurements than linear values ( Rogers, Manwell, & Wright, 2002 ).
Rare research attempts have been made of harvesting acoustic noise from an environment where the noise level is high and continuous, to transfer it into electrical energy. For example, a research team at the University of Florida examined acoustic energy conversion. They reported analysis of strain energy conversion using a flyback converter circuit ( Horowitz et al. 2002 ). The output of a vibrating PZT piezoceramic beam is connected to an AC to DC flyback converter, which is estimated to provide greater than 80 percent conversion efficiency at an input power of 1 mW and 75% efficiency at an input power of 200 μW ( Kasyap, Lim, et al. 2002 ). It was finalized that there is far too insufficient amount of power available from acoustic noise to be of use in the scenario being investigated, except for very rare environments with extremely high noise levels.
Human Power
Researchers have been working on many projects to generate electricity from active/passive human power, such as exploiting, cranking, shaking, squeezing, spinning, pushing, pumping, and pulling ( Starner & Paradiso, 2004 ). For example some types of flashlights were powered with wind-up generators in the early 20th century (US patent 1,184,056, 1916). Later versions of these devices, such as wind-up cell phone chargers and radios, became available in the commercial market. For instance, Freeplay’s (a commercial company) wind-up radios make 60 turns in one minute of cranking, which allows storing of 500 Joules of energy in a spring. The spring system drives a magnetic generator and efficiently produces enough power for about an hour of play.
A battery-free wireless remote control for Zenith televisions was another human-powered device. The design, called “Space Commander”, was introduced by Robert Adler in 1956. The system consisted of a set of buttons that hit aluminum material to produce ultrasound. The produced ultrasound energy was decoded at the television to turn it on, change channels and mute the volume ( Adler, Desmares, & Spracklen, 1982 ). Adler’s “Space Commander” design was then replaced by the active infrared remote controls and is being used in many current remote control systems.
Another similar architecture, developed by Paradiso and Feldmeier (2001) is a piezoelectric element, which was comprised of a resonantly matched transformer and conditioning electronics. This system was actuated when hit by a button, and it produced about 1mJ at 3V per 15N push. The generated power was enough to run a digital encoder and radio that was able to transmit over 50 feet. Materials used for this device were off-the-shelf components, which enabled placing compact digital controllers independently without any battery or wire maintenance.
An average human body burns approximately 10.5 MJ every day, which is equal to about 121W of power dissipation. Power dissipation occurs in the average human body either actively or passively in daily life motions, making the human body and motions an attractive ambient energy source. Researchers have proposed and conducted several studies to capture power from the human body. For example Starner has researched and investigated some of these energy- harvesting techniques to power wearable electronics ( Starner, 1996 ). MIT researchers considered these studies and suggested that the most reliable and exploitable energy source occurs at the foot during heel strikes when running or walking ( Shenck & Paradiso, 2001 ). This research initiated the development of piezoelectric shoe inserts capable of producing an average of 330 μW/cm2 while an average person is walking. The first application of shoe inserts was to power a low power wireless transceiver mounted to the shoe soles. The ongoing research efforts mostly focused on how to get power from the shoe, where the power is generated, to the point of interest or application. Such sources of power are considered as passive power sources in that the person is not required to put extra effort to generate power because power generation occurs while the person is doing regular daily activities, such as walking or running. Another group of power generators can be classified as active human-powered energy scavengers. These types of generators require the human to perform an action that is not part of the normal human performance. For instance, Freeplay has self-powered products that are powered by a constant-force spring that the user must wind up to operate the device ( FreePlay Energy, 2007 ). These types of products are very useful because of their battery-free systems.
For an RFID (Radio frequency identification) tag or other wireless device worn on the shoe, the piezoelectric shoe insert offers a good solution. However, the application space for such devices is extremely limited, and as mentioned previously, they are not very applicable to some of the low-powered devices, such as wireless sensor networks. Active human power, which requires the user to perform a specific power-generating motion, is common and may be referred to separately as active human-powered systems ( Roundy, 2003 ).
Conclusion
In conclusion, several currently developed, and overlooked ideas and options exist, and these can provide new energy resources to portable or wireless electronics devices within the energy-harvesting systems. The possibility of overall dependence on ambient energy resources may remove some constraints required by the limited reliability of standard batteries. Ambient energy harvesting can also provide an extended lifespan and support to conventional electronics systems. Students involved in this paper learned different ambient energy-harvesting, conversion, and storage systems. Students agreed to start a new research identify various ambient energy sources and design unique energy-harvesting systems.
Dr. Faruk Yildiz is an assistant professor in the Department of Agricultural and Industrial Sciences at Sam Houston State University, Huntsville Texas. He is a Member-at-large of Epsilon Pi Tau.
References
Adler, R., Desmares, P., & Spracklen, J. (1982). Ultrasonic remote control for home receivers, IEEE Trans. Consumer Electronics, 28 (1), 123–128.
Amirtharajah, R., & Chandrakasan, A. P. (1998). Self-powered signal processing using vibration-based power generation. IEEE Journal of Solid-State Circuits, 33 (5), 687-695.
DiSalvo, F. J. (1999). Thermoelectric cooling and power generation. Science, 285, 703-706.
FreePlay energy, (2007). Retrieved October 5, 2009, from http://www.freeplayenergy.com/products.
Holmes, A. S. (2004). Axial-flow microturbine with electromagnetic generator: Design, CFD simulation, and prototype demonstration. Proceedings of 17th IEEE International Micro Electro Mechanical Systems Conf. (MEMS 04), IEEE Press, 568–571.
Horowitz, S., Kasyap, A., Liu, F., Johnson, D., Nishida, T., Ngo, K., Sheplak, M., & Cattafesta, L. (2002). Technology development for self-powered sensors. Proceedings of 1st Flow Control Conference, St Louis.
Kasap, S.O. (2001). Optoelectronics and photonics: Principles and practices, New Jersey: Prentice-Hall.
Kasyap, A., Lim, J. S., Johnson, D., Horowitz, S., Nishida, T., Ngo, K., Sheplak, M., & Cattafesta, L. (2002). Energy reclamation from a vibrating piezoceramic composite beam. Proceedings of 9th Int. Conference on Sound and Vibration, Orlando.
Kulah, H., & Najafi, K. (2004). An electromagnetic micro power generator for low-frequency environmental vibrations. 17th IEEE International Conference on Micro Eletro Mechanical Systems (MEMS), 237-240.
Lang, S. B. (2005). Pyroelectricity: From ancient curiosity to modern imaging tool. Changes in the net dipole moment of certain materials form the basis for a broad range of IR detectors. Retrieved October 5, 2009, from http://www.physicstoday.org/vol-58/iss-8/p31.html
Marzencki, M. (2005). Vibration energy scavenging. European Commission research Project VIBES (IST-1-507911) of the 6th STREP Framework Program.
Meninger, S., Mur-Miranda, J. O., Amirtharajah, R., Chandrakasan, A. P., & Lang, J. H. (2001). Vibration-to-electric energy conversion. IEEE Transactions on Very Large Scale Integration (VLSI) Systems, 9 (1), 64-76.
Mitcheson, P. D., Green, T. C., Yeatman, E. M., & Holmes, A. S. (2004). Analysis of optimized micro-generator architectures for self-powered ubiquitous computers. Imperial College of Science Technology and Medicine. Exhibition Road, London, SW7 2BT.
Mikami, S., Tetsuro, M., Masahiko, Y., & Hiroko, O. (2005). A wireless-Interface SoC powered by energy harvesting for short-range data communication. IEEE 0-7803-9162-4/05 2005.
Paradiso, J., & Feldmeier, M. (2001). A compact, wireless, self-powered pushbutton controller. ubicomp: Ubiquitous Computing.
Pacific Northwest National Laboratory (PNNL). Available technologies (2007). Patent Pending, Battelle Number(s): 12398-E, 13664-B, Retrieved October 6, 2009, from http://availabletechnologies.pnl.gov/technology.asp?id=85
Pescovitz, D. (2002). The power of small technology. Smalltimes, 2 (1).
Rabaey, J. M., Ammer, M. J., Da Silva Jr, J. L., Patel, D., & Roundy, S. (2000). Picoradio supports ad hoc ultra-low power wireless networking. IEEE Computer, pp. 42–48.
Raffaelle, R., Underwood, J., Scheiman, D., Cowen, J., Jenkins, P., Hepp, A. F., Harris J., & Wilt, D. M. (2000). Integrated solar power systems. 28th IEEE Photovoltaic Specialists Conference, 1370-1373.
Roundy, S. J. (2003). Energy scavenging for wireless sensor nodes with a focus on vibration to electricity Conversion. A dissertation, The University of California, Berkeley.
Roundy, S., Steingart, D., Fréchette, L., Wright, P. K., & Rabaey, J. (2004). Power sources for wireless networks. Proceedings of 1st European Workshop on Wireless Sensor Networks (EWSN '04), Berlin, Germany.
Roundy, S., & Wright, P. K., & Pister, K. S. (2002). Micro-electrostatic vibration-to-electricity converters. Proceedings of the ASME International Mechanical Engineering Congress and Expo.
Roundy, S., Wright, P. K., & Rabaey, J. (2003). A study of low level vibrations as a power source for wireless sensor nodes. Computer Communications, 26, 1131-1144.
Roundy, S., Wright, P. K., & Rabaey J. (2004). Energy scavenging for wireless sensor networks with special focus on vibrations. New York: Kluwer Academic Publishers.
Roundy, S., & Wright, P. K. (2004). A piezoelectric vibration based generator for wireless electronics. Smart Materials and Structures, 13, 1131-1142
Rogers, A., L., Manwell, J. F., & Wright, S. (2002) PE, Wind turbine acoustic noise. Renewable Energy Research Laboratory, Department of Mechanical and Industrial Engineering, University of Massachusetts at Amherst.
Rowe, D. M. (1999). Thermoelectrics, an environmentally-friendly source of electrical power. Renewable Energy, 16, 1251-1256.
Shenck, N. S., Paradiso, J. A. (2001). Energy scavenging with shoe-mounted piezoelectrics, IEEE Micro, 21, 30-41.
Starner, T., & Paradiso, J. A. (2004). Human-generated power for mobile electronics. In C. Piguet (Ed). Low-power electronics design, chapter 45, 1–35, CRC Press, New York, NY.
Stevens, J. (1999). Optimized thermal design of small thermoelectric generators. Proceedings of 34th Intersociety Energy Conversion Eng. Conference. Society of Automotive Engineers, 1999-01-2564.
Sodano, H. A., Inman, D.J., & Park, G. (2004). A review of power harvesting from vibration using piezoelectric materials. The Shock and Vibration Digest, 36 (3), 197-205.
Skoog, D. A., Holler, J. F., & Crouch, S. R. (2006). Principles of Instrumental Analysis. (6th ed). Florence, KY: Cengage Learning, Brooks Cole.
Starner, T. (1996). Human-powered wearable computing. IBM Systems Journal, 35 (3), 618-629.
Stordeur, M., & Stark, I. (1997). Low power thermoelectric generator – Self-sufficient energy supply for micro systems. 16th International Conference on Thermoelectrics, 575 – 577.
Sterken, T., Fiorini, P., Baert, K., Puers, R., & Borghs, G. (2003). An electret-based electrostatic μ- generator. IEEE 0-7803-7731-1/03.
Self Contained Generating and Lighting Unit, (1916). US patent 1,184,056, Patent and Trademark Office, 1916.
Sun, W., Kherani, N. P., Hirschman, K. D., Gadeken, L. L., & Fauchet, P.M. (2005). A three-dimensional porous silicon p-n diode for betavoltaics and photovoltaics. Advanced Materials, 17, 1230-1233.
Thomas, J., Clark, J. W., & Clark, W. W. (2005). Harvesting energy from piezoelectric material. IEEE CS. University of Pittsburgh, 1536-1268.
Torres, E. O., Rincón-Mora, G. A. (2005). Energy-harvesting chips and the quest for everlasting life. IEEE Georgia Tech Analog and Power IC Design Lab.
Yaglioglu, O. (2002). Modeling and design considerations for a micro-hydraulic piezoelectric power generator. Master’s thesis, Department of Electrical Eng. and Computer Science, MIT.
Yildiz, F., Zhu, J., & Pecen, R., Guo, L. (2007). Energy scavenging for wireless sensor nodes with a focus on rotation to electricity conversion. American Society of Engineering Education, AC 2007-2254:
Yeatman, E.M. (2004). Advances in power sources for wireless sensor nodes. Proceedings of International Workshop on Wearable and Implantable Body Sensor Networks, Imperial College, 20–21. Exhibition Road, London, SW7 2BT.
TS