JOTS v36n2 - Introducing Engineering Design Through an Intelligent Rube Goldberg Implementation
Introducing Engineering Design Through an Intelligent Rube Goldberg Implementation
Sushil Acharya and Arif Sirinterlikci
Abstract
Engineering students need a head start on designing a component, a process, or a system early in their educational endeavors, and engineering design topics need to be introduced appropriately without negatively affecting students’ motivation for engineering. In ENGR1010 at Robert Morris University, freshmen engineering students are introduced to engineering design theory and practice through fun and challenging Rube Goldberg implementations to give them self-confidence early in their education. This article presents a background on Rube Goldberg mechanisms and their use in engineering education. However, the main focus is given to engineering design and microcontrollers in Rube Goldberg mechanisms. The authors worked with a multidisciplinary group of freshmen software and mechanical engineering students to complete an intelligent Rube Goldberg mechanism to assemble cheese sandwiches. The project was accomplished by using a 10-step design process and generating an automated assembly line with Rube Goldberg contraption elements controlled by a microcontroller. The Robot C programming language was employed for programming. The project details, project evaluation, and student responses are also included in this paper.
Implementation Background
The Accreditation Board for Engineering and Technology (ABET) and industry demand that engineering students be able to design, work in teams, and be effective communicators ( Feland & Fisher, 2002 ). One freshman engineering course at Robert Morris University entitled, “ENGR1010: Introduction to Engineering” was revised by the authors in order to introduce engineering students to the design process through an implementation of a Rube Goldberg device. A Rube Goldberg process is used to trigger and maintain student motivation for engineering because it provides a mechanism for “learning while having fun.” This design process facilitated teamwork and emphasized communication.
According to the Merriam-Webster Online Dictionary (2010) the Rube Goldberg concept is defined as "accomplishing by complex means what seemingly could be done simply.” This is how Reuben Lucius Goldberg, a Pulitzer Prizewinning artist, portrayed machines and gadgets as excessive for well over 50 years. In addition, he was sometimes skeptical about the technology upon which these devices were based . His cartoons combined simple machines and common household items to create complex and wacky contraptions that accomplished trivial tasks. While most machines work to make difficult tasks simple, his designs made simple tasks complex. For instance, he designed a simplified pencil sharpener, a safety device for walking on icy pavements; he dealt with problems like putting a stamp on an envelope, screwing in a light bulb, or making a cup of coffee in 20 or more steps. An example of one of his designs is illustrated in Figure 1 ( Rube Goldberg Inc., n.d. ).
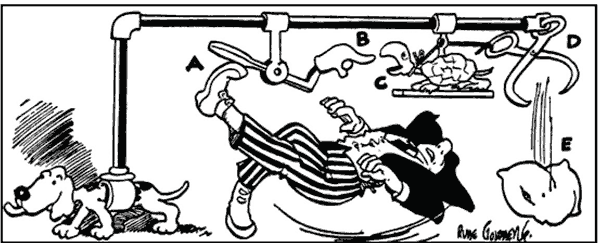
Figure 1. Safety device for walking on icy pavements: when you slip on ice your foot kicks paddle (A), lowering finger (B), snapping turtle (C) extends neck to bite finger opening ice tongs (D) and dropping pillow (E), thus allowing you to fall on something soft. ( Rube Goldberg Inc., n.d. )
Throughout the years more and more Rube Goldberg implementations have been seen. “ The Way Things Go ,” a 30-minute film produced in 1987 by Peter Fischli and David Weiss depicts 100 feet of physical interactions, chemical reactions, and precisely crafted chaos worthy of Rube Goldberg ( Fischli & Weiss, 1987 ). This Rube Goldberg implementation utilized fire as the main element to drive the chain reaction. “ The Cog ,” Honda Corporation’s two-minute commercial for their Accord model automobile, is yet another Rube Goldberg implementation used to present this product in an attractive way ( Easton, 2005 ).
Rube Goldberg’s work continues to connect with adult audience who are well immersed in modern technology; younger fans are also intrigued by the creativity and innovation factors involved in the designs ( Phi Chapter Theta Tau and Purdue University, n.d. ). Today Rube Goldberg inspires hobbies, regional and national competitions, and course-based projects in academia—examples include a playing card shuffling machine, a beverage can smashing contraption, a baby feeding mechanism, and a light bulb fitting device.
The most widely known Rube Goldberg competition is a national event held annually at Purdue University. The National Rube Goldberg Machine Contest has for 22 years invited teams of engineering students to design and build complex machines that perform basic chores. The competition brings Goldberg's inanimate cartoons to life in a way that moves students away from traditional methods of looking at problems and sends them deep into the intuitive but chaotic realm of imagination. The resulting inventions are collections of bits and pieces, parts of useless machines scraped together to achieve an innovative and imaginative contraption to resolve the problem at hand. The contest began as a rivalry between two Purdue engineering fraternities, and was popular at Purdue in the 1940s and 1950s. Since its revival in 1983, winners have appeared on various TV shows, including Jimmy Kimmel Live, Late Night with David Letterman, NBC's Today Show, CBS's This Morning, CBS News, Beyond 2000, CNN and ABC's Good Morning America ( Phi Chapter Theta Tau and Purdue University, n.d. ).
Similar mechanisms are made worldwide, but they are known by different names. In Japan, these contraptions are called “Pythagorean Devices,” named after the Greek Mathematician, Pythagoras. Such devices are shown in a 15-minute educational television program for kids called, Pythagora Switch , which encourages children to learn and to think. In the United Kingdom, they are named after a similar cartoonist, Heath Robinson, and there they are called Heath Robinson contraptions. Likewise, in Denmark, they are called Storm P. maskiner (Storm P. machines) after the Danish animator Robert Storm Petersen ( Rube Goldberg Machine, n.d. ).
Argonne National Laboratory defines a successful Rube Goldberg machine (the one that is competitive in Rube Goldberg machine contests) as a machine that combines a number of objective and subjective qualities that fulfill tasks, follow rules, and impress judges ( U.S. Department of Energy, n.d. ). Projects that depicted the following qualities are favored by the judges in these competitions:
- The machine completes its tasks without any (highly desired) or with minimal human intervention.
- The machine’s steps are clearly visible and are adequately explained during presentations.
- The machine has more antigravity power steps (highly desired) or it has a minimal number of gravity power steps.
- The machine is not entirely powered by electrical motors or uses minimal electrical power to move objects.
- The teams show strong team spirit
- The machine incorporates adequate safety features.
Rube Goldberg in Engineering Education
At a time when the United States is looking to inspire young minds, Rube Goldberg’s legacy represents the best in American innovation, humor, and unconventional thinking ( Phi Chapter Theta Tau and Purdue University, n.d. ). Engineering departments in U.S. universities are using Rube Goldberg for two purposes: to expose younger students to engineering and to encourage engineering students to think outside the box. Rube Goldberg “thinking” is a great way to teach basic principles of science like magnetism, gravity, and friction. In addition, Rube Goldberg projects also promote patience and discipline, and they can assist in maintaining students’ interest in science, mathematics, and engineering.
At Texas Tech University, Rube Goldberg engineering projects are used to teach students how to take an idea from paper and turn it into reality ( Texas Tech University, n.d. ). For the past eight fall semesters Texas Tech civil engineering students, mostly freshmen, have had a chance at devising Rube Goldberg machines. Students have carried out projects to accomplish very precise engineering tasks (e.g., leveraging a solid wooden cube onto a tall block and moving a small object two inches onto a platform). A pilot freshman curriculum has been designed and implemented in the Mechanical Engineering Department at the Rochester Institute of Technology ( DeBartolo & Robinson, 2007 ; McGowan, 2008 ). The course sequence gives freshmen an overview of a broad range of mechanical engineering activities. The first course gives students most of the basic tools they will need, and the second course is centered on an electromechanical Rube Goldberg design project, undertaken by the entire class. Students develop the design concept, build the system, and prove that it works. They are able to practice skills such as communications, teamwork, time management, and experimentation. At Carnegie Mellon University, a general robotics class requires students to design simple Rube Goldberg machines ( Rube Goldberg Challenge, 2006 ). The University of South Carolina (USC) is seeding a novel engineering curriculum in South Carolina middle and high schools as part of a national effort to expose younger students to vocational education. USC's Project Lead the Way program exhibits an elaborate Rube Goldberg apparatus in the basement of its mechanical engineering building ( Garriott, 2003 ). Finally, at Robert Morris University Rube Goldberg implementation is utilized as a course-based project in ENGR1010, an introductory freshman engineering course.
Rube Goldberg Projects at Robert Morris University
Since the fall of 2005, the Engineering Department at Robert Morris University has assigned Rube Goldberg projects in ENGR1010: “Introduction to Engineering.” Students are guided by the following constraints:
- Minimum 15 steps are required for the mission to be completed.
- Items easily found (not purchased) should be used as much as possible (highly desired).
- Worth of purchased items should not exceed $50.00.
- Minimum human intervention is encouraged and will result in higher grade (highly desired).
- Mechanical or electrical components/devices could be used to accomplish the task.
- Any food-related projects’ products should be edible.
- Live animals should be excluded from all designs.
Students work in teams of four or five and are required to follow a detailed engineering design and development approach. The steps of this approach are presented next:
- Inception (Problem Identification & Problem Statement Generation) : In this phase the teams study the problem at hand. They first gather the facts about the requirements and then they define the problem and its constraints.
- Conceptual Design (Alternative Concept Generation) : The teams generate alternative concepts as potential solutions. Sketches are accompanied with explanations.
- Product Design : After selecting the best feasible solution, adequately labeled engineering drawings of each component and the entire product are prepared in assembly form. The Bill of Materials (B.O.M.) is completed.
- Product Development : The Rube Goldberg contraption is fabricated.
- Product Testing & Implementation : Adjustments are made to improve the effectiveness of the solution during testing.
The teams are required to submit the following works throughout the project.
- Project Proposal : The teams submit an engineering proposal consisting of a problem statement, project objectives, a preliminary B.O.M., and a plan of action. This is due one week after the project is assigned.
-
Project Progress Updates
: The students provide a weekly update to the instructor and their team members, either via email or through prescheduled meetings. Altogether nine updates are required. In these updates the teams are required to communicate the following:
- What happened during the past week?
- What will happen this week?
- What are the major issues the team is facing?
- Project Report : At the end of the project duration (12 academic weeks) the teams submit comprehensive project reports. Each report provides the details of how the project is executed. It contains an abstract, the project’s objectives, the plan of action, a Gantt chart depicting the management plan (including tasks, resources, and timeline), and an important section on discussion and results. In this section, the students describe each step of the design and how it supported the Rube Goldberg mechanism. Students are also required to include a summary section on the project postmortem.
-
Project Presentation: At the end of the project duration (12 academic weeks) the teams present their product to the class and guests. The presentation consists of both a PowerPoint Presentation and a successful execution demonstration of the Rube Goldberg mechanism. Students are evaluated by the instructor and by their peers. Time durations and rules for the presentation include the following:
- Total Time: 15 minutes per team—10-minute PowerPoint presentation, 5 minutes for Q & A session following the presentation.
-
Presentation of the working implementation.
- Explanation of each important component in detail.
- Successful demonstration of the working implementation after three attempts.
Because the Rube Goldberg implementation process is heavily based on creativity, students are asked to use all of their imaginations to come up with a design that functions, is feasible within the cost constraints, and is fun to work with. In the past, students have used electricity (AC and/or DC), hydropower, robots, and simple weight-based mechanisms to build their projects.
In addition to the criteria briefly discussed previously, the students are required to accomplish the following elements:
- Communication : The team members are required to effectively communicate with each other to ensure the success of their project. Project proposal, team meetings, project construction, project progress updates, and the project report provide mechanisms for team communications.
- Teamwork : The teams are required to practice the five growth stages of a team: “Forming, Storming, Norming, Performing, and Adjourning.” The teams are told that “No teamwork means no successful project” and “A successful project that lacks teamwork is a failed project.” The team meetings, project construction, and project demonstration provide mechanisms for teamwork. Team members are also encouraged to bring up matters that are counterproductive to the team in a timely manner. However, they are requested to resolve these matter among themselves, and the instructor will intervene only as a last resort.
- Recycle : The teams are encouraged to utilize previously used items, which are easily found (but not purchased).
- Fun Factor : Teams are encouraged to enjoy the process as they go through the engineering design and development steps. It is believed that the fun factor helps establish ownership of the project and gives the students a passion for completing the projects.
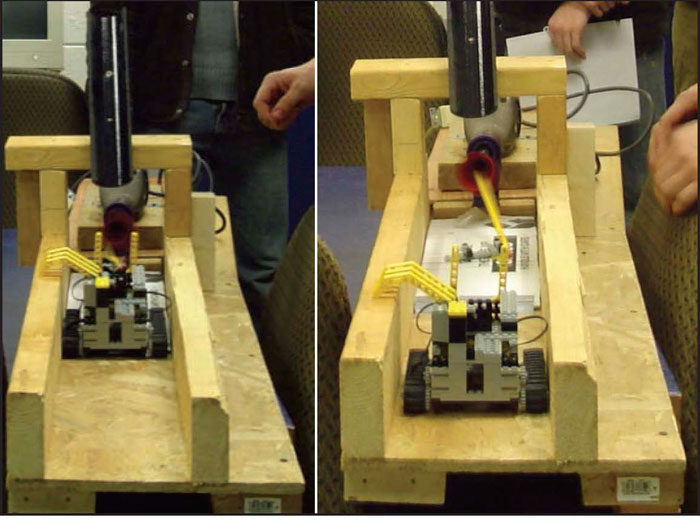
Figure 2. LEGO Mindstorms equipment being utilized for a Rube Goldberg mechanism for sharpening pencils.
Over the years, students have worked on projects that make scrambled eggs, sharpen pencils, crush empty soda cans, and assemble cheese sandwiches. A wide variety of means have been employed by the students, including robotics (as shown in Figure 2). Other project examples using more conventional means are illustrated in Figure 3. In this article, the authors present in detail an intelligent Rube Goldberg device that makes use of a VEX Robotics Development System to assemble a cheese sandwich.
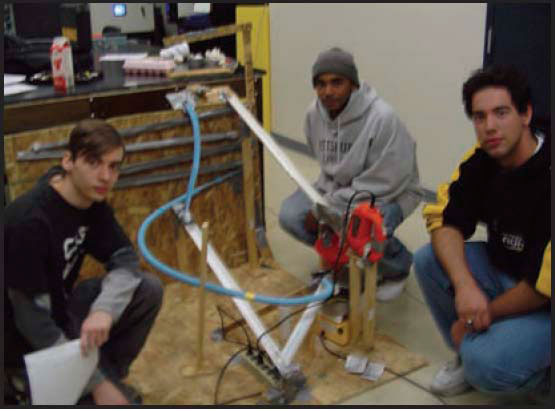
Figure 3. A Rube Goldberg project with conventional means used for frying eggs.
Intelligent Rube Goldberg
The Center for Intelligent Machines (n.d.) at McGill University defines intelligent machines as “machines capable of adapting their goal-oriented behavior by sensing and interpreting their environment, making decisions and plans, and then carrying out those plans using physical actions.” Along the same lines the authors define an Intelligent Rube Goldberg as a machine that is capable of accomplishing a Rube Goldberg goal through physical actions initiated through the interpretation of environmental data obtained through sensors. During fall of 2008, students in ENGR1010 were assigned a Rube Goldberg project with an objective of assembling a cheese sandwich made from two slices of sandwich bread and one slice of cheese. The students were guided by the rules and requirements listed in the previous section. Ninety percent of the grade was allocated for accomplishing the given set of requirements, and 10% of the grade was designated for creativity. Although different groups used intelligences and experiences in different areas, one group decided to control the Rube Goldberg mechanism with a microcontroller meeting the definition of an Intelligent Rube Goldberg machine. The group members explained their design concept by stating, “Where most teams built a traditional elaborate mechanism, our team uses software to accomplish the task at hand.”
The authors recommended that the students use the VEX Robotics Development System. A conveyor was built using the tank threads of the VEX Robotics Development System (as shown in Figure 4). This solution was chosen due to a system’s ability of being consistent in terms of placing the bread and cheese slices at the same locations in repeated operation. This is the automation principle of repeatability. While the conveyor was driven by a DC VEX motor, dispensers were actuated by VEX servomotors. Wood and PVC were utilized in the conveyor frame and the dispensers. Along the conveyor four VEX limit switches were placed, and these would be tripped by the plate used for the sandwich assembly. Three identical dispensers were designed and placed above the conveyor for dispensing the bread slices and the cheese slice. Each dispenser operated by a servomotor that flipped the lever of the dispenser, thereby dropping the bread or cheese onto the plate. Appropriate time delays are applied before each critical activity of the control sequence. Details of the design are illustrated and explained in the following section.

Figure 4. Intelligent Rube Goldberg mechanism/cheese sandwich assembly line.
The intelligent machine used the following 17 steps to meet its goal. These steps are labeled in Figure 4:
- Flip the microcontroller switch – The machine is turned ON and the levers are reset.
- During the 10-second interval (time delay) the machine is loaded with bread and cheese slices.
- DC motor starts (motor[port1]) and plate begins moving along the conveyor.
- First limit switch (touchSensor1) is triggered by the plate.
- The conveyor belt stops.
- The servomotor turns ON (motor[port2]), flipping the lever and the first slice of bread falls.
- The belt begins moving again with the bread on the plate.
- The second limit switch (touchSensor2) is triggered by the advancing plate.
- The conveyor belt stops.
- The second servomotor turns ON (motor[port3]), flipping the lever and the cheese slice falls.
- The conveyor belt starts moving again with the plate, bread, and cheese.
- The third limit switch (touchSensor3) is triggered by the advancing plate.
- The conveyor belt stops.
- The third servomotor turns ON (motor[port4]), flipping the lever and the second slice of bread falls.
- The conveyor belt starts moving again, and the cheese sandwich assembly moves toward the final limit switch.
- The fourth limit switch (touchSensor4) is tripped.
- The conveyor stops (motor[port1]), presenting the plate and the cheese sandwich assembly at the edge of it.
A block diagram of the process is depicted in Figure 5. In terms of the programming efforts, Carnegie Mellon University’s Robot C programming environment and language was used. Since one of the team members was a software engineering major, the team took advantage of his expertise in programming. The program syntax is listed in the Appendix A.

Figure 5. IBlock diagram for the logic sequence.
Rube Goldberg Judges’ Evaluation and Students’ Feedback
Based on the Argonne National Laboratory criteria listed previously, the Intelligent Rube Goldberg implementation was evaluated:
- The machine completes its tasks without any (highly desirable) or with minimal human intervention: This criterion is met. Once the program is initiated, the software modules control the overall execution of the required steps. Human intervention is not necessary.
- The machine’s steps are clearly visible and are adequately explained during presentations: This criterion is met. The steps are clearly labeled in the program code as well as in the physical implementation.
- The machine has more antigravity power steps (highly desired) or with minimal number of gravity power steps: This criterion is not applicable as this implementation is executed by a controller through a program code.
- The machine is not entirely powered by electrical motors or uses minimal electrical power to move objects: This criterion contradicts the authors’ definition of intelligent Rube Goldberg. Being an intelligent device, it utilizes power that is controlled through a program code.
- The team shows strong team spirit: This criterion is met. The teamwork depicted was exceptional. The strengths and weaknesses of the team members were adequately utilized resulting in a successful implementation of the device.
- The machine incorporates adequate safety features: This criterion is met. The implementation does not provide any safety hazards due to the design and the process parameters.
At the end of the project, the students were required to perform a self/peer evaluation and project reflection. The questions asked and some of the student feedbacks are listed in Table 1:
1. What did you learn from this project experience?
|
2. How will you use this experience to improve personally and professionally?
|
3. If you were to go back in time what would you do differently?
|
Conclusions
This intelligent Rube Goldberg project provided a unique engineering design experience for the students. Instead of using traditional devices and gadgets to accomplish the goal of making a cheese sandwich, a microcontroller with programming ability and multiple sensors were used. Students successfully accomplished the task by strictly following authors’ guidelines and the recommended detailed engineering design and development approach. All required work products were submitted and presented within the deadline. Students were evaluated for communication, teamwork, recycling, and fun factors. The team communicated amongst themselves daily and with the instructor weekly. They kept a log of their communications. During the presentations team members excelled by properly explaining all the steps and then successfully demonstrating their machine. The teamwork observed by members of this team was exceptional. Roles were clearly defined and timely executed. During the course of the project all three team members remained engaged and successfully completed their allocated tasks. As previously mentioned, one member conducted the programming tasks, while the other two members designed and assembled electrical and mechanical elements of the intelligent Rube Goldberg contraption. On top of their individual roles, members also learned from the expertise of one another. The budget for this machine was minimal, and the bulk of the budget was used for fresh cheese and bread. Students borrowed the VEX Robotics Development System from the engineering laboratories and the PVC pipes and wood were picked up from scrap storage of the RMU Engineering Department. As a note on creativity, the students used VEX tank treads to develop their conveyor for the mechanism.
Student feedback during and after the learning experience were positive. The students were observed having fun while working on the project. The project was voted one of the best by the observers, and because of its compactness it is currently being used by the RMU Engineering Department as a demonstration project for visitors.
A project of this nature, where a system, a component, or a process is designed through fun-filled and challenging activities, gives students a better understanding of the work of an engineer and assists in maintaining students’ interest in engineering. Students are able to capitalize on their early exposure to engineering design and related activities as they perform in other course-based projects throughout their engineering education. An early start thus enhances students’ design skills and makes them more confident and competitive.
Dr. Sushil Acharya is an Assistant Professor of Software Engineering in the School of Engineering, Mathematics, and Science at Robert Morris University.
Dr. Arif Sirinterlikci is an Associate Professor of Engineering and Director of Engineering Laboratories at Robert Morris University School of Engineering, Mathematics, and Science, Moon Township, Pennsylvania. He is a Member-at-large of Epsilon Pi Tau.
References
Center for Intelligence Machines (n.d.), Center for Intelligence Machines, McGill University. Retrieved August 22, 2009 from http://www.cim.mcgill.ca/
DeBartolo, E., & Robinson, R. (2007). A freshman engineering curriculum integrating design and experimentation, International Journal of Mechanical Engineering Education, 35 , (2), pp. 91-107
Easton, J. (2005), The Honda COG commercial you won't see on television. Retrieved from http://www.tabloidcolumn.com/honda-accord-cog.html
Feland, J. M., & Fisher, C. (2002). Cramming twenty pounds more into a sophomore design toolkit: Increasing curricular loads on design students and enjoying it! 2002 ASME curriculum innovation award honorable mention, Retrieved August 24, 2009, from http://files.asme.org/asmeorg/Governance/Honors/1104.pdf
Fischli, P., & Weiss, D. (1987). The way things go . Retrieved August 24, 2009, from http://icarusfilms.com/cat97/t-z/the_way.html
Garriott, C. (2003). USC Engineering leads the way . The Daily Gamecock, University of South Carolina. Retrieved August 29, 2009 from http://media.www.dailygamecock.com/media/storage/paper247/news/2003/06/25/News/Usc-Engineering.Leads.The.Way-446874.shtml
McGowan, M. (2008). Engineering students flex mechanical muscles, demonstrate Rube Goldberg machines , Retrieved August 29, 2009 from http://media.www.dailytoreador.com/media/storage/paper870/news/2008/10/06/LaVida/Engineering.Students.Flex.Mechanical.Muscles.Demonstrate.Rube.Goldberg.Machines-3470113.shtml
Phi Chapter Theta Tau and Purdue University (n.d.), Rube machine contest . Retrieved July 12, 2009, from http://www.rubemachine.com
Rube Goldberg. (2010). In Merriam-Webster Online Dictionary . Retrieved July 8, 2009 from http://www.merriam-webster.com/dictionary/rube goldberg
Rube Goldberg Challenge (2006), Lessons Engineering 101, Retrieved July 14, 2009, from URL http://www.education.rec.ri.cmu.edu/roboticscurriculum/vex_online/curriculum/engineering_101/activities/docs/goldberg_challenge.pdf
Rube Goldberg Inc. (n.d.), Rube Goldberg. Retrieved July 8, 2009 from http://www.rubegoldberg.com
Rube Goldberg Machine (n.d.), Academic Dictionaries and Encyclopedias. Retrieved July 9, 2009 from http://dic.academic.ru/dic.nsf/enwiki/128943
Texas Tech University (n.d.), Rube Goldberg engineering, Texas Tech today . Retrieved July 24, 2009 from http://www.depts.ttu.edu/communications/news/stories/videos/rube-goldberg.php
U.S. Department of Energy (n.d.), What makes a good Rube Goldberg machine? Rube Goldberg Machine Contest, Argonne National Laboratory. Retrieved July 10, 2009, from http://www.anl.gov/Careers/Education/rube/goodrubes.html
Appendix A – Syntax of the ROBOT C program
task main () { motor[port2]=-127; motor[port3]=-127; motor[port4]=-127; wait1Msec(10000); while(SensorValue(touchSensor4)==0) { motor[port1]=35; if(SensorValue(touchSensor1)==1) { motor[port1]=0; motor[port2]=127; wait1Msec(2000); motor[port2]=-127; wait1Msec(2000); while(SensorValue(touchSensor4)==0) } motor[port1]=35; } } if(SensorValue(touchSensor2)==1) { motor[port1]=0; motor[port3]=127; wait1Msec(2000); motor[port3]=-127; wait1Msec(2000); while(SensorValue(touchSensor4)==0) } motor[port1]=35; } if(SensorValue(touchSensor3)==1) { motor[port1]=0; motor[port4]=127; wait1Msec(2000); motor[port4]=-127; wait1Msec(2000); while(SensorValue(touchSensor4)==0) } motor[port1]=35; } } } SensorValue(touchSensor4)=1; Motor[port1]=0; }