JOTS v37n2 - Printing Processes Used to Manufacture Photovoltaic Solar Cells
Printing Processes Used to Manufacture Photovoltaic Solar Cells
Tina E. Rardin and Renmei Xu
Abstract
There is a growing need for renewable energy sources, and solar power is a good option in many instances. Photovoltaic solar panels are now being manufactured via various methods, and different printing processes are being incorporated into the manufacturing process. Screen printing has been used most prevalently in the printing process to make solar cells, but some companies have used the offset web press type methods to put material onto foil; they also have created solar cells with inkjet printing. The printing of solar cells has helped to reduce manufacturing costs in most cases, and it also has increased the various applications in which solar power both is and can be used. Many more options for photovoltaic solar panels are available, and not simply the traditional ones that are often placed on rooftops. Such a variety of solar panels are partially to the result of the implementation of suitable printing processes during the production of these cells.
Introduction
With ever-increasing political and economic oil conflicts as well as climate change, a growing need for renewable energy that comes from natural resources, such as sunlight, wind, rain, tides, and geothermal heat, is warranted. Wars have been caused in part to protect oil supplies, and millions of tons of pollutants and greenhouse gases are emitted into the atmosphere every year due to the burning of fossil fuels to create energy. There is no other area of technology than renewable energy technologies that can both “meet the challenges of climate change and secure an energy supply in an intelligent manner” ( Wengenmayr & Bührke, 2008 , p. 1). A number of options for new technologies of renewable energy exist, that is, from geothermal to wind to hydrogen fuel cells to hydropower; however, one of the most accessible and widely used technologies is solar energy. Solar power does not create any noise when it is working, “is non-polluting, does not generate greenhouse gases, and creates no waste products,” ( Brenner, 2010 , p. 27), which is also why it is an increasingly preferred renewable energy. Additionally, the potential for solar power is immense. The energy from the sunlight that strikes the earth for only forty minutes is equal to the global energy consumption for an entire year ( Zweibel, Mason, & Vasilis, 2008 ). All of that energy is of no use, unless it can be captured. A good method to harness this immense amount of energy and thus to eventually use it as electricity is through the use of photovoltaic (PV) energy systems.
Photovoltaic Power
According to the U.S. Department of Energy (2010, p. 1) , “the diversity, adaptability, and modularity of PV technology make it distinct from other renewable resources.” Solar photovoltaic power is extremely useful because it can be produced in a number of ways from a variety of materials, and it can be used for numerous applications. Photovoltaic cells can be used for anything (e.g., from a small strip that powers a simple calculator to personal panels on homes to larger commercial settings and solar farms spread out over vast areas of land). Photovoltaic modules are also useful since they have minimal maintenance costs and are extremely long lasting; some manufacturers offer up to 25-year warrantees ( Brenner, 2010 ). In 2008, photovoltaic systems were the largest producer of electricity directly from solar energy in the world, in terms of kWh produced per year ( Vanek & Albright, 2008 ).
The photovoltaic or PV cell is a type of technology that uses semiconducting materials to convert the energy in sunlight into usable electricity. Derived from Greek, the term photovoltaic can be translated as “electrical energy from light” ( Wengenmayr & Bührke, 2008 , p. 42). The cells transfer the energy of the photons penetrating the solar panels to electrons that are “channeled into an external circuit for powering an electrical load” ( Vanek & Albright, 2008 , p. 249). A PV panel is made up of multiple photovoltaic cells, anywhere from 50 to 120, which are connected together in an electrical circuit that can then be connected to an exterior circuit at a single point. An entire PV system often is comprised of a number of panels, so that a greater, more desirable amount of voltage is produced. These PV cells take on many forms and are produced in a number of different ways, often including various printing processes.
Printing Solar Cells
In order to make the use of solar power a likely alternative to fossil fuels, it needs to be economically comparable to conventional energy sources like coal, natural gas, and oil. This matter of cost is the largest issue facing the success of photovoltaic solar panel use. Efficiency of solar cells is the percentage that they are efficient at “converting the radiation from the sun into electricity for the area of the active part of the module” ( Brenner, 2010 , p. 29). Efficiency is possibly the most important factor when determining the overall use and quality of a solar cell, and it can play a large role in reducing overall costs. The two main strategies to reduce the cost of power production in photovoltaic devices are to increase efficiency and to lower production costs of the starting materials ( Wengenmayr & Bührke, 2008 ). Implementing different printing processes throughout certain steps of manufacturing has recently helped to accomplish both efficiency and lower costs. Certain printing processes like screen printing, inkjet printing, and even web press offset printing lend themselves to being just what is needed to make various types of solar cells. These processes are becoming a large part of solar-cell manufacturing for different kinds of photovoltaic solar energy, each with its own benefits and drawbacks. It is important to understand the different types of solar cells and materials that are used to make them in order to understand where these printing processes can fit in.
Traditional PV Material
Conventional solar cells are made from silicon, are flat plated and rigid, and generally have the highest efficiencies. Crystalline silicon (c-Si) is the most widely used and most efficient material expended in the production of photovoltaic solar cells, with commercial efficiencies sometimes reaching 20%. It is estimated that about 80% of all photovoltaic solar panels are created with crystalline silicon, and this material is especially useful because it has shown both long-term performance and reliability ( Applied Materials, 2010 ). Crystalline silicon cells are made from silicon wafers that can be either mono-crystalline or multi-crystalline structures, depending on what is available or what is needed for that particular process. All structures using pure silicon will face shortages, especially since the material is used in other semiconductor industries as well as in solar PV. Silicon is a plentiful element in the earth’s crust, but most of it occurs in compounds that would be costly to extract the pure silicon from them ( Vanek & Albright, 2008 ). Crystalline silicon has been the go-to material to make efficient solar panels; however, because of shortages and the general high costs of silicon, other options have been developed with other materials or smaller amounts of silicon.
Thin Film PV Materials
Thin film solar cells offer the best option in terms of producing solar cells. Thin film solar cells require less semiconductor material, so material costs are substantially reduced ( Zoomer, 2010 ). The versatility of applications with thin film could also vastly increase the use of solar power. While numerous different materials have been used for thin film, the most widely used at present are amorphous silicon, organic polymers, and a combination of conductive metals including compounds of copper, indium, diselenide, and sometimes gallium.
In terms of the more conventional materials, amorphous silicon (a-Si) can be mass produced more easily than crystalline silicon, and it can be very thin, even to the point of being flexible, so much smaller amounts are required ( Vanek & Albright, 2008 ). Since the atoms are not arranged in any particular order, like in a crystalline structure, there is more flexibility with what can be made with amorphous silicon. The material is full of defects naturally so impurities are not a problem, and it can be applied uniformly over very large surfaces, making it more usable than crystalline silicon. Amorphous silicon does not have the same quality of electrical properties as crystalline silicon, but the gap has been closed in recent years ( Amorphous Semiconductors Research Group, 2010 ).
Several combinations of conductive and semiconductive metals and compounds can be used to create solar cells, but the most acclaimed and most common seems to be one consisting of copper indium diselenide, also known as CIS ( Goetzberger, Knobloch, & Voss, 1998 ). As early as 1978, high efficiencies without degradation were observed, which made this a very important material in the thin film solar industry. Recently, a similar but even more productive combination of copper, indium, selenium, and gallium, also known as CIGS, has been used ( Inslee & Hendricks, 2008 ). These materials help to make the mass production of solar cells more of a reality, and since CIGS can potentially have similar efficiencies to traditional cells, about 19.5% ( Contreras, et al., 2005 ), this is one of the most promising new PV technologies.
A company called Konarka Technologies has developed thin film solar PV cells from organic polymers in the form of “Power Plastic.” These organic photovoltaics are a third-generation type of solar power that uses a photo-reactive polymer that can be combined with several other very thin layers to be used in a number of products. The Power Plastic can be printed on large rolls of flexible substrates, is made from recyclable materials, and converts light to energy both outdoors from the sun and indoors from a light bulb ( Konarka Technologies, 2010 ). Another application of organic polymers is seen when it is used as a dye that is a combination of nanoparticles that convert light to electricity ( Fraunhofer-Gesellschaft, 2008 ). Both of these applications of organic polymers immensely help reduce the cost of manufacturing solar cells, but they are not as efficient as silicon based cells, and the longevity is not known of these new cells.
Screen Printing
The basic principle of the process of screen printing is simply the use of a stencil to reproduce the same image over and over again. This is currently conventionally done with the use of a mesh screen coated with light-sensitive emulsion that is then exposed to light with the desired positive image blocked, and then washed out to create the mesh stencil. There are other ways to make the stencil, but the use of photographic emulsion is most common. Ink is then applied to the screen and pushed through with a squeegee to transfer the ink on the open image area to the desired substrate. This process can be repeated as many times as the screen materials will last. Screen printing is one of the most versatile printing processes because almost anything from glass to paper to fabric to plastic can be printed on, and a very thick amount of ink can be laid down, unlike in other printing processes. A number of factors should be considered when screen printing is used, depending on the type of materials and images that are being printed. Factors including mesh count, screen angle, emulsion-on-mesh thickness, stencil surface smoothness, ink type, how detailed the image is, how many impressions the screen can last, and squeegee pressure can all affect the overall quality of the product that is being printed. This screen-printing process has been used as part of the process to make conventional silicon solar cells due to its versatile nature.
According to Peter Brenner (2010) , global marketing manager of photovoltaics for DuPont Microcircuit Materials, “Screen printing photovoltaic cells is the most reliable method and fastest growing application in industrial printing” (p. 26). Screen printing is also the most commonly and conventionally used printing process throughout the manufacture of photovoltaic solar cells. In fact, over 90% of all crystalline silicon modules are manufactured using screen printing, and about 60% of flexible thin film modules use screen printing in the manufacturing process ( Brenner, 2010 ).
The way that screen printing is used in the process of making solar cells is that PV solar cells are often metalized through a screen-printing process. This is the application of three different types of metallization pastes onto the c-Si cell. The first paste is the front-side silver used on the side facing the sun; it makes up the collector gridlines and the silver bus bars, and the second is the rear-side tabbing silver or silver-aluminum, and the third is the rear-side aluminum paste that actually reacts with the silicon to create the back surface field ( Brenner, 2010 ). The screen-printing process is especially useful in applying these pastes since consistency in each application as well as the ability to lay down different thicknesses for the different types of pastes are both very important. However, according to Brenner (2010) , similar to screen printing any object, a number of variables involved in screen-printing photovoltaics must be monitored: ink composition (solid content, viscosity, rheology, evaporation rate, dispersion), press setup (squeegee durometer and shape, attack angle, squeegee pressure, print speed, snap off, registration control), screen/stencil (mesh count, wire diameter, percent of open area, emulsion thickness, mesh tension), and the environment (room temperature, humidity, air turbulence, cleanliness, substrate surface, shelf life of ink and screens). Each of these variables is generally something that should be considered in any type of screen printing, but it is especially important with printing PV modules due to the nature of the materials and the accuracy that is needed.
Another way that screen printing is utilized in the manufacture of solar panels is through the use of organic dye, a combination of nanoparticles, which serves as a semiconductor to convert sunlight to energy. The versatility of this dye allows for different colors and designs to be printed, making this an excellent option to be integrated into the façade of a building or to serve as a decorative element. These panels could be integrated into windows and not only convert sunlight to electricity but also serve as a sunshade to the interior of the building, saving additional energy. Even though screen-printing this dye onto glass makes it an excellent choice for building integration, the cells only have an efficiency of about 4%, so they are not yet competitive with conventional silicon panels. The longevity of this technology is yet to be determined, though it did seem to perform well in initial tests ( Fraunhofer-Gesellschaft, 2008 ). Even with these drawbacks, this organic dye could be a very popular choice by consumers due to its more aesthetically pleasing qualities and consumers’ options to have whatever design or color they desire.
Inkjet Printing
Inkjet printing is one of the newest and most experimental methods used to make solar cells, and it could potentially have a very big role in making solar panels accessible to everyone. The most common type of personal computer printers use inkjet technology, and it is also used widely in industrial applications such as the production of numerous microscopic items, the formation of conductive traces for circuits, and the manufacture of color filters in LCD and plasma displays ( Clark, 2008 ). Inkjet printing is a non-impact printing that uses a number of nozzles to spray ink droplets directly onto the paper or substrate without touching it ( Tyson, 2010 ). This basic principle makes inkjet printing very useful in that not only can it spray onto a number of different surfaces, but also it can spray onto a number of materials. It is not simply conventional printing ink that can be sprayed. Inkjet printing recently has been used in the production of both flexible thin film solar cells as well as more conventional rigid silicon cells.
Using inkjet printing to apply semiconductive material onto flexible substrates that could result in the formation of a thin film PV solar cell has the potential to become available to any person who has an inkjet printer. While this is not the case yet, many places are using inkjet printing to reduce manufacturing costs and trying to increase efficiencies of thin film solar cells. Konarka Technologies is using inkjet printing as part of the production process of their Power Plastic thin film solar cells, which are made of organic polymers. This material has been in production and development for a few years, and in 2008, inkjet printing was used, making the process much cheaper than it previously had been ( Masamitsu, 2008 ). This paper thin plastic has infinite possibilities and can be applied to any flexible surface such as tents, umbrellas, and handbags, but there are a few drawbacks. The efficiency of this inkjet printed material is only 3-5%, so to get anywhere near the amount of energy a conventional silicon solar cell can get, there would need to be a very large area available to lay down this Power Plastic. These cells also only last about a couple of years, as opposed to decades that conventional cells last ( Bullis, 2008 ). These drawbacks currently limit the use of the product, but the benefits are still very great since potentially anyone could print these cells. That may be a few years away, but the versatility and massive amount of places this plastic could be used are not to be taken lightly. Inkjet printing has played an important role in helping to make this happen.
Inkjet printing is also now being used in place of screen printing to make electrical connections during the process of making more conventional crystalline silicon solar modules. The inkjet method can be more precise than previous methods, and since the print heads do not make contact with the silicon, a thinner, more fragile piece can be used. Conventional screen printing methods need to use silicon wafers that are at least 200 micrometers thick because any thinner wafer will likely break. It is estimated that 100 micrometers of silicon can be used with this inkjet process, and since silicon can account for 75% of the total cost of materials and production, this could greatly reduce overall costs ( Bullis, 2009 ). The silver gridlines can be printed with inkjet printing and the ink used is more conductive than the silver paste in screen printing. Maikel van Hest, a scientist at the National Renewable Energy Laboratory, noted more precise lines of 35 to 40 micrometers wide, compared with 100 to 125 micrometers wide with screen printing can also be printed ( Bullis, 2009 ). This ultimately means that not as much silver will need to be used, saving additional money and resources. The thinner lines also can block less of the solar collecting material, so that the sun’s radiation can hit more of the surfaces that are actually collecting it, as opposed to bouncing off because of the thicker silver lines. These thinner lines make the cells more efficient, although at the moment the amount of increased efficiency is unknown.
No matter what application inkjet printing is being used in, the process is proving to be a very important part of making photovoltaic solar cells more economical and more accessible. While currently it is only used in mass production, the potential of being able to print on a personal printer is definitely a considerable advantage that this process has over any of the others. Not only is inkjet printing improving already-developed PV manufacturing processes, but it is also a key component to an entirely new type of thin film that could be used for any number of purposes. Inkjet printing is helping to reduce costs of manufacturing and increase the efficiency and availability of solar cells, which are currently vital goals of the photovoltaic solar industry.
Web Printing
Though not exactly using the principle of offset lithographic printing, there are companies using web press applications to coat semiconducting materials onto flexible substrates. The substrates that are currently being used are plastics and metal foils. Offset printing is a type of planography, because the plates used during printing are completely flat. The principle of offset lithography is that the oil-based ink only sticks to the hydrophobic image area on the plate, which is transferred to a blanket, and then transferred onto the substrate. Web offset printing is a continuous process that prints on rolls of substrates, though it is still an indirect process due to the nature of offset lithographic printing. Newspapers, for instance, are often printed by an offset web press and then cut down into the necessary sheets. With the manufacture of solar cells, certain principles of web offset printing are applied, and they are shown to greatly decrease costs and increase production capabilities.
Nanosolar is a company that prints the semiconductive compound of copper, indium, gallium, and selenium (CIGS) onto thin foil. The company uses a web press application and “can produce a hundred feet of continuously rolled solar cell per minute” ( Inslee & Hendricks, 2008 , p. 72). Their nanoparticle ink mixture, consisting of CIGS and the necessary components for proper dispersion, is coated onto “a specially-prepared proprietary alloy of metal foil using high-throughput coating/printing techniques” ( Nanosolar, 2010 , paragraph 4). This method of printing has replaced the conventional process of high-vacuum deposition, which is much more time consuming. Nanosolar has taken the economics and processes of printing and applied them to the formation of solar cells and seems to have done so very successfully. Their process should make this type of solar cell electricity as cheap as the current electricity taken off the grid ( Inslee & Hendricks, 2008 ). The National Renewable Energies Laboratory certifies that their solar cells have up to a 15.3% efficiency ( Nanosolar Communications, 2009 ), which is comparable to conventional crystalline silicon cells. The product itself is also thin and flexible, which could be useful in a number of applications. Nanosolar’s thin film cells are much more economical than traditional silicon cells, and they can be mass-produced very quickly thanks to the use of a printing process.
Konarka's Power Plastic uses not only inkjet printing but also a web press application in some instances. they use a type of coating process that is continuously rolled to get the right substrate combination of usable photographic film and organic polymers ( Bullis, 2008 ). Though not exactly a printing process, this application is most definitely inspired by traditional web printing, and this is an important part of the process of the manufacture of Power Plastic.
Web press applications are fairly new to the photovoltaic solar cell industry, but they are playing a very important role in the ability of the industry to use mass-production processes. This ultimately makes the cells more economical, and in the case of Nanosolar, the cells are fairly comparable in efficiency. The use of web printing is definitely a help for the solar-cell industry.
Conclusions
In these times of uncertain energy sources and with the impacts that they are having on the atmosphere, clean, renewable solar energy is a good alternative. However, it is still more expensive than methods used currently by consumers, and inn order to be a viable option, it has to be attainable and affordable. With the use of different materials and thin film technologies, the use of photovoltaic solar energy for the average person is becoming more of a reality.
Printing processes have helped the photovoltaic solar industry by providing useful solutions to decrease manufacturing costs and increase the availability of these technologies to consumers. Screen printing has been used for years as a good option for metallization when producing traditional crystalline silicon solar cells, and it has more recently been used as the means of applying organic semiconducting dye to make photovoltaic solar cells. Inkjet printing is useful in the production of solar cells as both a new replacement for the screen-printing metallization and in the manufacturing of thin film solar cells. Even web offset printing has inspired some of the processes used to make thin film solar cells, and it is a very effective way to mass-produce these cells quickly. Each of these processes has helped to make solar cells more affordable and attainable.
Thin film solar cells would not be as widely produced and researched if it were not for the printing processes that helped make them as useful as they currently have become. Conventional crystalline silicon solar cells are efficient and have great longevity, but they cannot be used everywhere since they are rigid; they also are very expensive and resource intensive to produce. Thin film seems to be the direction that the people who make solar cells are heading, and if they can get equal efficiencies then there is no reason why these cells should not be used as replacements for conventional energy methods. Thin film cells also can be used on roofs, but they can also be placed just above anywhere and are more aesthetically pleasing, which would make them more marketable than conventional solar panels. There are a number of new developments in the photovoltaic solar industry, and with the help of processes inspired by the printing industry, this industry will continue to develop, and eventually PV cells will be a highly sought-after energy source.
Tina Rardin is currently a Production Coordinator at Pratt Corporation in Indianapolis, Indiana.
Dr. Renmei Xu is an Assistant Professor in the Department of Technology at Ball State University, Muncie, IN.
References
Amorphous Semiconductors Research Group (2010). Amorphous silicon. Retrieved from http://www.ayil.hacettepe.edu.tr/pages/Amorphous/Amorphous%20silicon.html
Applied Materials (2010). The world's most efficient solar cells. Retrieved from http://www.appliedmaterials.com/technologies/solar/crystalline-silicon
Brenner, P. (2010). Printing photovoltaics. Industrial + Specialty Printing, 1(01), 26-33.
Bullis, K. (2008). Mass production of plastic solar cells. Technology Review. Retrieved from http://www.technologyreview.com/energy/21574/page1/
Bullis, K. (2009). Ink-jet printing for cheaper solar cells. Technology Review. Retrieved from http://www.technologyreview.com/energy/22599/page2/
Clark, E. (2008). Solar cells created with inkjet technology. Gizmag. Retrieved from http://www.gizmag.com/solar-cells-created-with-inkjet-technology/9094/
Contreras, M. A., Ramanathan, K., Abushama, J., Hasoon, F., Young, D. L., Egaas, B., & Noufi, R. (2005). Diode characteristics of state-of-the-art ZnO/CdS/Cu(In1-xGax)Se2 solar cells. Progress in Photovoltaics: Research and Applications, 13: 209.
Fraunhofer-Gesellschaft (2008, January 31). Screen-printed solar cells in many colors and designs, even used in windows. ScienceDaily. Retrieved from http://www.sciencedaily.com/releases/2008/01/080130194130.htm
Goetzberger, A., Knobloch, J., & Voss, B. (1998). Crystalline silicon solar cells. Weinheim: Wiley.
Inslee, J., & Hendricks, B. (2008). Apollo’s fire: Igniting America’s clean energy economy. Washington: Island Press.
Konarka Technologies (2010). Konarka’s paradigm-shifting technology. Retrieved from http://www.konarka.com/index.php/technology/our-technology/
Masamitsu, E. (2008). Startup makes cheap solar film cells . . . with an inkjet printer. Popular Mechanics. Retrieved from http://www.popularmechanics.com/science/energy/solar-wind/4253464
Nanosolar (2010). Production process. Retrieved from http://www.nanosolar.com/technology/production-process
Nanosolar Communications (2009, January 9). NREL certifies 15.3% Nanosolar foil efficiency. Retrieved from http://www.nanosolar.com/company/blog#68
Tyson, J. (2010). How inkjet printers work. Retrieved from http://computer.howstuffworks.com/inkjetprinter.htm
U.S. Department of Energy (2010). Photovoltaics. Retrieved from www.eere.energy.gov/solar/pdfs/43684.pdf
Vanek, F. M., & Albright, L. D. (2008). Energy systems engineering: Evaluation & implementation. New York: McGraw Hill.
Wengenmayr, R., & Bührke, T. (Eds.) (2008). Renewable energy: Sustainable energy concepts for the future. Weinheim: Wiley-VCH.
Zoomer, W. (2010). Contemporary thin-film solar cells. Industrial + Specialty Printing, 1(03), 18-21.
Zweibel, K., Mason, J., & Vasilis, F. (2008, January). Solar grand plan. Scientific American. 64-73.
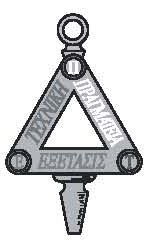